چهار دسته جرثقیل سقفی وجود دارد:
- جرثقیل سقفی تک پل
- جرثقیل سقفی تک پل آویز
- جرثقیل سقفی تک پل دیواری
- جرثقیل سقفی دو پل
هر یک از این انواع برای کاربردهای خاصی طراحی و ساخته شده اند که در زیر به طور مختصر توضیح داده شده است.
جرثقیل سقفی تک پل
جرثقیل سقفی تک پل نوعی جرثقیل است که شامل یک تیر یا پل تنها میباشد که عرض محدوده عملیاتی جرثقیل را در بر میگیرد. این پل روی دو تراک انتهایی نصب شده است که جرثقیل را در طول مسیر ریلی حرکت میدهند. مکانیزم بالابری، که به آن بالابر گفته میشود، در طول لبه پایینی پل حرکت میکند. این تنظیم یکی از رایجترین انواع جرثقیلهای مورد استفاده در تولید، انبارداری و برنامههای نگهداری به دلیل سادگی، صرفهجویی در هزینه و انعطافپذیری آن است. در اینجا برخی از جنبههای کلیدی جرثقیلهای سقفی تک پل آورده شده است:
اجزاء
- پل: اصلیترین جزء ساختاری که عرض جرثقیل را در بر میگیرد. این بخش بالابر و ترولی را پشتیبانی میکند.
- تراکهای انتهایی: در هر دو انتهای پل قرار دارند و چرخهایی را در خود جای دادهاند که اجازه میدهند جرثقیل در طول راهآهن حرکت کند.
- بالابر: جزء بلند کننده که بار را بالا و پایین میبرد. این قسمت در طول پل حرکت میکند.
- ترولی: مکانیزمی که بالابر را در طول پل حمل میکند و اجازه حرکت جانبی بار را میدهد.
- راهآهن: ریلهایی که جرثقیل روی آن عملیات انجام میدهد، معمولاً روی دیوارها یا ستونهای تأسیسات نصب میشوند.
- سیستم کنترل: میتواند یک کنترل آویز، ریموت بیسیم یا سیستم کنترل شده از کابین باشد که به اپراتور اجازه میدهد حرکات و عملکردهای بالابر جرثقیل را کنترل کند.
مزایا
- صرفهجویی در هزینه: جرثقیلهای تک پل به طور کلی از جرثقیلهای دو پل ارزانتر هستند به دلیل طراحی سادهتر و نیاز کمتر به مواد برای ساخت.
- انعطافپذیری و سازگاری: طراحی آنها اجازه نصب در تأسیسات با فضای سرپوشیده محدود یا فضای کف محدود را میدهد.
- آسانی نصب و نگهداری: سادگی طراحی آنها باعث میشود نصب و نگهداری آنها آسانتر و سریعتر باشد.
معایب
- ظرفیت محدود: آنها معمولاً برای بارهای سبکتر (معمولاً تا ۲۰ تن، اما برخی مدلها میتوانند تا ۵۰ تن را نیز تحمل کنند) و دهانههای کوتاهتر (تا حدود ۳۰ متر یا ۹۸ پا) طراحی شدهاند.
- ارتفاع قلاب پایینتر: طراحی تک پل ممکن است ارتفاع قلاب کمتری نسبت به طراحی دو پل ارائه دهد، که میتواند در برخی کاربردها محدودیت باشد.
کاربردها
جرثقیلهای سقفی تک پل در صنایع مختلفی استفاده میشوند، از جمله:
- تأسیسات تولیدی برای جابجایی مواد اولیه، قطعات و محصولات نهایی.
- انبارها برای انباشتن و بازیابی کالاها.
- کارگاهها برای نگهداری و تعمیر تجهیزات و وسایل نقلیه.
- کارخانههای فولاد و ریختهگریها برای دست زدن به مواد مذاب با طراحیهای ویژه بالابر و ترولی.
این نوع جرثقیل یک جزء حیاتی در بسیاری از سیستمهای جابجایی مواد است و راهحلهای بلند کردن کارآمد، قابل اعتماد و صرفهجویی در هزینه را برای برنامههای صنعتی متعدد فراهم میکند.
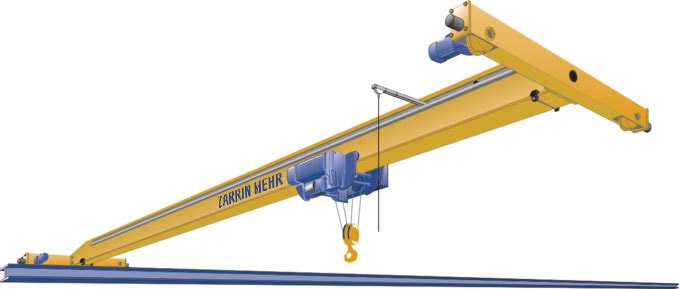
جرثقیل سقفی تک پل زرین مهر
جرثقیل سقفی تک پل زرین مهر یک قطعه تجهیزات بسیار کارآمد برای جابجایی مواد است که قادر به بلند کردن بارها تا ۱۶ تن میباشد. این امر آن را برای طیف وسیعی از صنایع مناسب میسازد. با توانایی امتداد تا ۳۹ متر، حتی در ساختمانهایی با ارتفاع سقف پایین نیز به طور مؤثر عمل میکند و فاصله ایمنی از سقف کارخانه را تضمین میکند. طراحی بدنه زرین مهر جرثقیلها حداکثر استفاده از فضای عمودی موجود را امکانپذیر میسازد و نیاز به ساخت و ساز اضافی را کاهش میدهد.
سری جرثقیلهای سقفی زرین مهر شامل انواع پیوستهای جانبی میشود که سازگاری و انعطافپذیری را در پیکربندیهای مکانی موجود افزایش میدهد. این بخشهای کوچک به کاربران امکان میدهد تا بیشترین ارتفاع قلاب را به دست آورند. برای ساختمانهای جدید، نسخه سوم این جرثقیل یک راهکار ایدهآل ارائه میدهد با فراهم کردن حداقل فاصله مورد نیاز و دسترسی حداکثری به قلاب. علاوه بر این، سری جرثقیلهای زرین مهر با طیف وسیعی از لوازم جانبی مجهز شدهاند تا از کاربردهای متنوع پشتیبانی کنند، و آن را به یک گزینه چندمنظوره و مؤثر برای شرکتها تبدیل مینماید.
راهحلهای اتصال دهنده پل به تراک انتهایی برای جرثقیلهای سقفی تک پل:
آیا نگرانیهایی در مورد محدودیتهای ارتفاع سقف کارخانه یا کارگاه خود دارید که ممکن است نصب یک جرثقیل سقفی تک پل استاندارد را دشوار سازد؟ دیگر جای نگرانی نیست!
شرکت مهندسی جرثقیل زرین مهر، طیف گستردهای از راهحلهای اتصال پل به تراک انتهایی را پیشنهاد میدهد. این راهحلها عبارتند از:
جرثقیل سقفی تک پل آویز
جرثقیل سقفی تک پل آویز (که به آن جرثقیل زیرآویز نیز گفته میشود) نوعی تجهیز برای جابجایی مواد در داخل یک مکان است. در ادامه، توضیحات دقیقتری در مورد اجزاء، نحوه عملکرد و کاربردهای آن ارائه میشود:
اجزاء
- پل: اصلیترین جزء سازهای که عرض فضای کاری را دربرمیگیرد. در جرثقیل با عملکرد از زیر، پل معمولاً یک تیر تک است که مکانیزم بلند کردن را پشتیبانی میکند. این تیر در زیر لبههای تیرهای راهانداز حرکت میکند.
- تراکهای انتهایی: در هر دو انتهای پل قرار دارند و چرخهایی را در خود جای دادهاند که امکان حرکت جرثقیل را بر روی تیرهای راهانداز فراهم میکنند. در سیستمهای با عملکرد از زیر، تراکهای انتهایی بر روی لبههای پایینی تیرهای راهانداز حرکت میکنند.
- بالابر: مکانیزم بلند کردن که بالا و پایین پل حرکت میکند. شامل موتور، درام، طناب سیمی یا زنجیر و قلاب بلندکننده است. بالابر جزءی است که واقعاً بار را بلند و پایین میکند.
- تیرهای راهانداز: تیرهای موازی که جرثقیل را پشتیبانی میکنند. معمولاً بر روی سقف یا بخش بالایی از محیط کار نصب میشوند و امکان حرکت جرثقیل سقفی با عملکرد از زیر را در مسیر مشخصی فراهم میکنند.
- سیستم کنترل: میتواند شامل یک کنترل آویز از جرثقیل، کنترل از راه دور بیسیم، یا کنترل از داخل کابین باشد. این سیستم به اپراتور امکان کنترل حرکت جرثقیل و بالابر را میدهد.
عملکرد
جرثقیلهای سقفی تک پل آویز برای کارهای سبک تا متوسط طراحی شدهاند. عملکرد آنها شامل:
- بلند و پایین کردن: بالابر با دقت بار را بلند و پایین میکند که توسط اپراتور از طریق سیستم کنترل کنترل میشود.
- حرکت افقی: جرثقیل به صورت افقی بر روی تیرهای راهانداز حرکت میکند که امکان قرار گرفتن بالابر را در هر نقطهای از دامنه جرثقیل فراهم میکند.
- حرکت ترولی: بالابر، که بر روی یک ترولی نصب شده، میتواند به عقب و جلو بر روی پل حرکت کند که امکان قرارگیری دقیق بارها را فراهم میکند.
مزایا
- کارآمدی فضایی: نیاز به فضای کمتری نسبت به جرثقیلهای با عملکرد از بالا دارند، که آنها را برای امکانات با محدودیت فضا ایدهآل میکند.
- انعطافپذیری: مناسب برای امکانات با سقفهای پایین یا موانع متعدد.
- مقرون به صرفه: به طور کلی نصب آنها نسبت به جرثقیلهای با عملکرد از بالا به دلیل نیاز کمتر به پشتیبانی ساختاری، هزینه کمتری دارد.
محدودیتها
- ظرفیت: معمولاً به بارهای سبکتر محدود میشوند، معمولاً تا 10 تن، اما میتواند بسته به طراحی متفاوت باشد.
- دامنه: دامنه محدودتری نسبت به جرثقیلهای با عملکرد از بالا دارند به دلیل ساختار پشتیبانی و استحکام تیر.
کاربردها
جرثقیلهای سقفی تک پل آویز در صنایع و امکانات مختلفی که فضا محدود است یا ساختار ساختمان امکان پشتیبانی از جرثقیلهای با عملکرد از بالا را ندارد، استفاده میشوند. کاربردها شامل:
- کارخانههای تولیدی: برای خطوط مونتاژ، جابجایی مواد، یا کاربردهای نگهداری.
- انبارها: برای جابجایی کالاها، به ویژه در مناطقی با فضای کف محدود.
- خودروسازی: برای جابجایی اجزاء در فرآیند مونتاژ.
- هوافضا: برای جابجایی قطعات ظریف در مناطق مونتاژ.
جرثقیلهای سقفی تک پل آویز ابزارهای ضروری در بسیاری از صنایع هستند که انعطافپذیری، کارآمدی و دقت در جابجایی مواد را ارائه میدهند. طراحی و عملکرد آنها آنها را به یک راهحل قابل اعتماد برای طیف گستردهای از کاربردها، به ویژه در فضاهای محدود یا جایی که فضای بالای سر محدود است، تبدیل میکند.
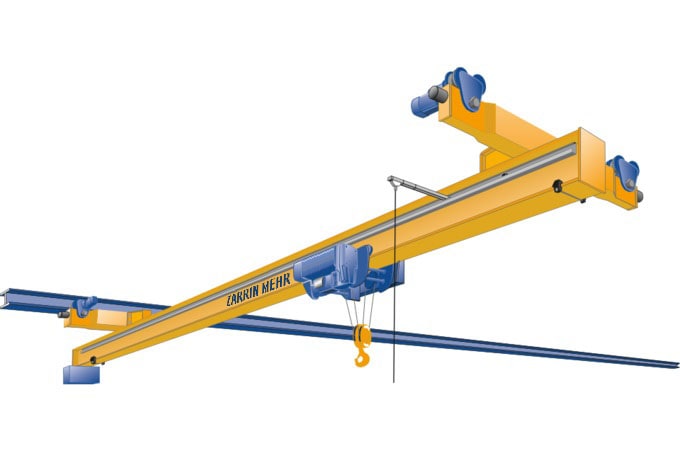
جرثقیل سقفی تک پل آویز زرین مهر
برای برآورده ساختن نیازهای پیچیده برخی سازهها، راهحلهای تخصصی ضروری هستند. جرثقیلهای سقفی تک پل آویز زرین مهر با کنترل آویز، یک راهحل عملی و کارآمد ارائه میدهند. این جرثقیلها طوری طراحی شدهاند که بدون نیاز به ستونهای حمایتی یا پشتیبانیهای تیر جداگانه، در زیر تیر سقف حرکت کنند، و حتی در فضاهایی با محدودیتها و قیدها، عملکرد بهینهای ارائه دهند.
جرثقیلهای سقفی تک پل آویز زرین مهر برای فضاهای کوچک سفارشیسازی شدهاند و دارای اتصالات سفارشی بر روی تیر اصلی و دسترسی برتر قلاب هستند. این طراحی استفاده از عرض امکانات را به حداکثر میرساند، و قرار دادن پل جرثقیل بین دو کاروان انتهایی، قلاب را در بالاترین مکان ممکن خود قرار میدهد.
جرثقیلهای تک پل آویز زرین مهر به طور معمول بارهایی تا ۸ تن را پشتیبانی میکنند و میتوانند تا ۲۵ متر دهانه داشته باشند. با این حال، شرکت نیز قادر به طراحی و ساخت جرثقیلها برای ظرفیتهای نامحدود و دهانههای سفارشی است. بسته به طراحی انتخابی، پل اصلی میتواند از یک بخش پروفیل غلتکی یا یک تیر جعبهای مقاوم در برابر پیچش ساخته شود. تمام نسخهها با برنامه تامین جامع برای لوازم جانبی و قطعات یدکی همراه هستند، که توسط تیم فنیهای با تجربه زرین مهر مدیریت میشود.
گزینههای اتصال پل به تراک انتهایی برای جرثقیلهای سقفی تک پل آویز:
اگر در مورد اینکه آیا ساختار سقف کارخانه یا کارگاه شما قادر به پشتیبانی از جرثقیلهای سقفی معمولی با عملکرد از زیر است، سوال دارید، خیالتان راحت باشد.
شرکت مهندسی جرثقیل زرین مهر، انتخاب گستردهای از جایگزینهای اتصال برای متصل کردن تیر به تراک انتهایی ارائه میدهد که شامل گزینههای زیر است:
جرثقیل سقفی تک پل دیواری
جرثقیل سقفی تک پل متحرک دیواری نوعی جرثقیل تخصصی طراحی شده برای جابجایی مواد در کارگاهها، انبارها، و محیطهای تولیدی است که در آنها بهینهسازی فضا حیاتی است. برخلاف جرثقیلهای سقفی سنتی که در امتداد تیرهای راهانداز نصب شده بر بالای اتاق حرکت میکنند، جرثقیلهای متحرک دیواری بر روی دیوارهای کناری نصب میشوند. این طراحی به آنها اجازه میدهد تا به طور همزمان با جرثقیلهای پل سقفی کار کنند، استفاده از فضا را به حداکثر رسانده و کارایی عملیاتی را افزایش میدهند. در اینجا نگاهی دقیقتر به ویژگیها، نحوه عملکرد، و کاربردهای آنها ارائه میشود:
ویژگیها
- ساختار تک پل: این جرثقیل شامل یک تیر (پل) است که بالابر و ترولی را حمل میکند. سادگی طراحی آن به صرفهجویی در هزینه و آسانی نگهداری کمک میکند.
- ریلهای نصب شده بر دیوار: جرثقیل در امتداد ریلهایی که بر روی دیوارهای امکان نصب شدهاند، حرکت میکند، اغلب در ارتفاعی که اجازه میدهد زیر جرثقیلهای سقفی موجود کار کند.
- سیستم بالابر و ترولی: مجهز به بالابری که به صورت عمودی حرکت میکند و ترولی که به صورت افقی در امتداد پل حرکت میکند، این امکان را فراهم میآورد که بارها را با دقت موقعیتدهی کند.
عملکرد
عملکرد جرثقیل سقفی تک پل متحرک دیواری با توانایی حرکت جانبی آن در امتداد ریلهای نصب شده بر دیوار مشخص میشود، که پوشش اضافی را فراهم میکند که با محدوده کاری جرثقیلهای ثابت یا پل تکمیل میشود. این ویژگی به ویژه در کارخانههایی با فضای کف محدود یا جایی که نیاز به ظرفیت بلندکردن اضافی بدون تداخل با سیستمهای اصلی جرثقیل سقفی وجود دارد، مفید است. جرثقیل از طریق یک کنترل آویز، کنترل رادیویی/از راه دور، یا ایستگاه کنترل عملیاتی میشود، که به اپراتور اجازه میدهد بارها را به صورت ایمن و کارآمد جابجایی دهد.
مزایا
- صرفهجویی در فضا: با استفاده از فضای عمودی بر روی دیوارها، این جرثقیلها فضای کف را برای سایر عملیاتها آزاد میکنند.
- انعطافپذیری: میتوان آنها را در ساختمانهای جدید نصب کرد یا به ساختارهای موجود تعبیه کرد، ارائه انعطافپذیری در طراحی و برنامهریزی.
- افزایش کارایی: پشتیبانی بلندکردن اضافی را فراهم میکند، کمک به بهبود عملیات و کاهش بار کاری بر روی جرثقیلهای اصلی.
نکات قابل توجه
- ظرفیت بار: معمولاً برای بارهای سبکتر نسبت به جرثقیلهای سقفی مستقل طراحی شدهاند، اغلب تا 5 تن.
- دامنه و دسترسی: دامنه و ظرفیت بلندکردن توسط استحکام ساختاری دیوار و طراحی جرثقیل محدود میشود.
- نیازمندیهای نصب: دیوارهای امکان باید قادر به پشتیبانی از ریلهای جرثقیل و بارهای دینامیکی ایجاد شده در حین عملیات باشند.
کاربردها
- جرثقیل ایستگاه کاری: ایدهآل برای انجام وظایف در ایستگاههای کاری خاص یا در طول خطوط تولید که مواد نیاز به حرکت موازی با دیوارهای کارگاه دارند.
- جرثقیل تکمیلی: به عنوان یک دستگاه بلندکردن تکمیلی عمل میکند که در مناطقی که توسط جرثقیلهای سقفی اصلی پوشش داده نشدهاند، کار میکند و کارایی کلی عملیات جابجایی مواد را افزایش میدهد.
- بهینهسازی فضا: مناسب برای امکاناتی که به دنبال حداکثر استفاده از فضای موجود بدون کاهش در تواناییهای بلندکردن هستند. میتواند در فضاهای باریک بین دیوار و ماشینآلات کار کند.
جرثقیلهای دیواری تک پل سقفی، راهکاری نوآورانه و مؤثر برای توسعه قابلیتهای بلندکردن و بهبود فرآیندهای جابجایی مواد در فضاهای صنعتی به شمار میروند. طرحبندی منحصربهفرد این جرثقیلها، امکان بهرهبرداری از آنها را حتی در کمترین فضاها میسر میسازد و این جرثقیلها را به عناصری ضروری و ارزشمند در محیطهای صنعتی پرترافیک و با چالشهای فضایی تبدیل میکند.
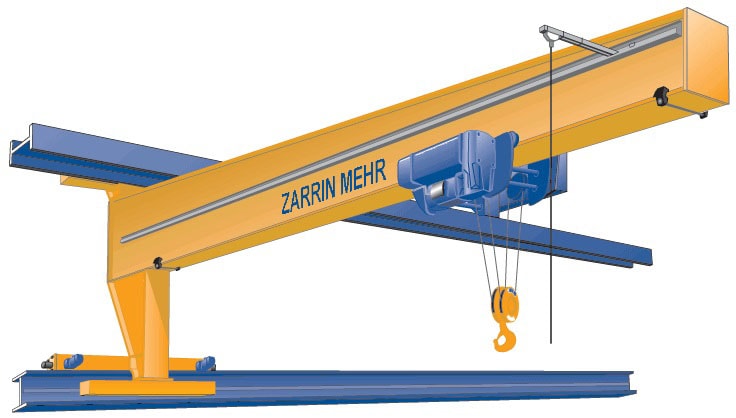
جرثقیل سقفی تک پل دیواری زرین مهر
جرثقیلهای سقفی تک پل دیواری زرین مهر با طراحی منحصر به فرد خود برای حرکت در مسیرهای خاصی در سطوح پایینتر نسبت به جرثقیلهای سقفی معمولی طراحی شدهاند. این قرارگیری استراتژیک به آنها امکان میدهد تا به طور مؤثر مواد را در نواحی مجزا از تولید جابجا کنند. طراحی آنها تضمین میکند که این جرثقیلها میتوانند به طور مستقل عمل کنند، بدون اختلال از یا به سیستمهای بزرگتر جرثقیل سقفی که معمولاً در محیطهای صنعتی یافت میشوند.
این جرثقیلها با ظرفیت بار تا ۵ تن و قابلیت افزایش دسترسی تا ۱۲ متر، ابزارهایی چندمنظوره برای طیف گستردهای از کاربردها هستند. توانایی جابجایی بارها در بخشهای محدود یا تخصصی از امکان، کارایی عملیاتی و انعطافپذیری را به ویژه در محیطهایی که بهینهسازی فضا حیاتی است، افزایش میدهد.
طراحی شده برای عملکرد استثنایی، جرثقیلهای دیواری متحرک زرین مهر نوآوری در فناوری جابجایی مواد را نمایش میدهند. طراحی مقاوم آنها نه تنها نیازهای مختلف وظایف صنعتی را برآورده میسازد، بلکه راهحلی قابل اتکا برای افزایش بهرهوری در نواحی که توسط سیستمهای جرثقیل سقفی سنتی سرویس داده نمیشوند، ارائه میدهد.
جرثقیل سقفی دو پل
پل جرثقیل سقفی دو پل از دو تیر فولادی تشکیل شده است که به صورت موازی با یکدیگر اجرا میشوند. این پیکربندی جرثقیل امکان حرکت مکانیزم بلندکردن، که اغلب به آن بالابر گفته میشود، را بر روی ریلهای نصب شده بر روی این دو پل فراهم میکند. در اینجا ویژگیها و جنبههای کلیدی جرثقیلهای سقفی دو پل آورده شده است:
ساختار و اجزا
- دو پل: دو پل موازی پایهای محکم و پایدار برای جرثقیل فراهم میکنند. آنها عرض محدوده کاری را در بر میگیرند و توسط تراکهای انتهایی در هر دو طرف پشتیبانی میشوند که امکان حرکت کل جرثقیل را بر روی راهانداز فراهم میکنند.
- بالابر و ترولی: بالابر، که کار بلند کردن را انجام میدهد، بر روی ترولی نصب شده است. این ترولی در امتداد پلها حرکت میکند که امکان حرکت جانبی بار را فراهم میآورد.
- راهانداز: راهانداز مجموعهای از ریلها است که موازی با پلها هستند و جرثقیل در امتداد آنها در داخل امکان به جلو و عقب حرکت میکند.
- تراکهای انتهایی: اینها در هر دو طرف پلها قرار دارند و حرکت جرثقیل را بر روی راهانداز ممکن میسازند.
- پل: پل شامل دو پل، ترولی و بالابر است. این اصلیترین بخش بلندکردن جرثقیل است.
مزایا
- ظرفیت بار بیشتر: جرثقیلهای دو پل میتوانند وزن بیشتری نسبت به جرثقیلهای تک پل تحمل کنند، که آنها را مناسب برای کاربردهای سنگین میکند.
- دامنه افزایش یافته: آنها میتوانند فاصلههای وسیعتری را بدون نیاز به پشتیبانی در میانه، که در امکاناتی که فضا و مانع نگرانیهایی هستند، مفید است، طی کنند.
- ارتفاع قلاب بهتر: طراحی امکان ارتفاع قلاب بیشتری را فراهم می کند چرا که بالابر میتواند بین یا روی پلها قرار گیرد، فضای بلندکردن عمودی بیشتری ارائه میدهد.
- سفارشیسازی و لوازم جانبی: آنها میتوانند با ویژگیهای اضافی مانند پیادهروها، کابینها و کنترلهای سرعت متغیر برای دستکاری دقیق مجهز شوند.
کاربردها
جرثقیلهای سقفی دو پل در تنظیمات متنوعی استفاده میشوند، از جمله:
- کارخانههای تولیدی و امکانات صنعتی برای جابجایی ماشینآلات یا مواد سنگین.
- انبارها و مراکز لجستیک برای دستکاری کالاهای حجیم.
- کارگاههای ساخت کشتی و بنادر برای بلند کردن اجزای بزرگ.
- کارخانههای فولاد و ریختهگریها برای حمل مواد اولیه و محصولات نهایی.
نکات انتخاب
هنگام انتخاب یک جرثقیل سقفی دو پل، نکاتی از جمله حداکثر ظرفیت بار، دامنه، ارتفاع بلندکردن، نیازهای سرعت، چرخه کاری، و شرایط خاص محیط کاری مانند دما، رطوبت و حضور مواد خورنده باید در نظر گرفته شوند.
این نوع جرثقیل نمایندهی یک سرمایهگذاری قابل توجه در زیرساختهای عملیاتی است، ظرفیت و انعطافپذیری افزایش یافته برای دستکاری بارهای سنگین را ارائه میدهد. نگهداری مناسب و پروتکلهای ایمنی ضروری برای تضمین طول عمر و عملکرد ایمن جرثقیلهای سقفی دو پل است.
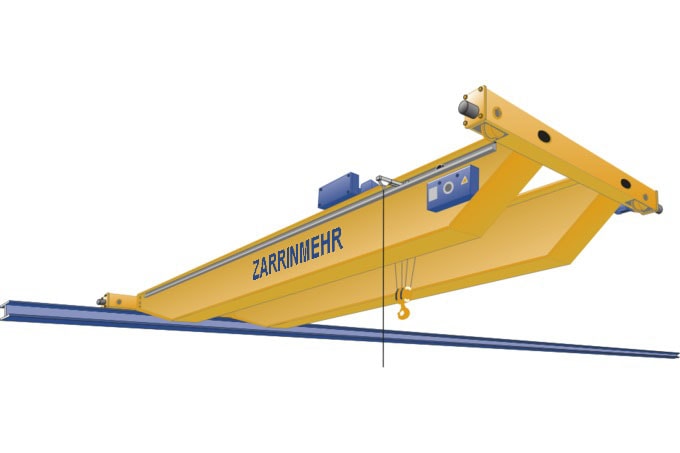
جرثقیلهای سقفی دو پل زرین مهر:
زرین مهر با جرثقیلهای سقفی دو پل خود، بلندکردن صنعتی را به ارتفاعات جدیدی میبرد، طراحی شده برای جابجایی آسان بارهای سنگین تا ۱۲۰ تن در سراسر مناطق وسیع. با بهرهگیری از مهندسی محکم مشاهده شده در جرثقیلهای دروازهای خود، این جرثقیلهای دو پل با ساختارهای معاصر و قدیمی به طور یکپارچه ادغام میشوند، با تشکر از گزینههای اتصال سازگار که پلها را به کاروان انتهایی متصل میکند. آنها به عنوان نمونههایی از قابلیت اطمینان قرار دارند، عملکرد بینظیر، انعطافپذیری و کاربرپسندی را ارائه میدهند.
فراتر از تواناییهای اصلی خود، زرین مهر با مجموعهای سفارشی از تجهیزات طراحی شده برای کاربردهای خاص، راهحلهای بلندکردن خود را غنیتر میکند، شامل انتخاب جامعی از لوازم جانبی و قطعات یدکی. پلهای جرثقیلهای سقفی دو پل ما از جعبههای دقیق جوشکاری شده ساخته شدهاند، که عملکرد برتر با وزن کم، دوام افزایش یافته، و کارایی هزینه را تضمین میکند. هر جزء، از جمله پلها و کاروانهای انتهایی، از طریق تجزیه و تحلیل روش المان محدود (FEM)، با پشتیبانی از تکنیکهای کامپیوتری پیشرفته، بهینهسازی میشود.
با دهانههایی که تا ۴۰ متر امتداد دارند، جرثقیلهای ما در کارخانه مهندسی جرثقیل زرین مهر طراحی و ساخته شدهاند، دارای ظرفیت نامحدود و ابعاد قابل تنظیم برای پاسخگویی به نیازهای بلندکردن منحصر به فرد و چالشبرانگیز. با گزینههایی برای افزایش سرعت، پلتفرمهای نگهداری یکپارچه، کاروانهای تخصصی، و راهروهای خدماتی با آسانسور، جرثقیلهای سقفی دو پل زرین مهر نمادی از برتری مهندسی هستند، طراحی شده برای ارتقای کارایی عملیاتی شما به نقطه اوج.
Bridge to End Carriage Connection Options for Double Girder Overhead Cranes:
If you’re concerned about whether your facility’s ceiling height can support conventional double girder overhead cranes, ZARRIN MEHR Crane Engineering Company has you covered. We offer a versatile array of connection solutions to seamlessly integrate girders with end-carriages, ensuring our cranes can be tailored to fit the unique structural constraints of your factory or workshop. Explore our diverse connection options designed with flexibility in mind.
Latest Completed Projects
Zarrin Mehr Crane Engineering Company has completed over 210 successful projects in various fields such as single girder overhead cranes, under running single girder overhead cranes, wall mounted overhead cranes, double girder overhead cranes, gantry cranes, jib cranes, material handling equipment, winches, elevators, machine tools, bending and cutting machines, and equipment for various industrial applications such as construction, manufacturing, and logistics.
Considering buying an overhead crane?
Frequently Asked Questions (FAQs)
What is an overhead crane?
An overhead crane, also known as a bridge crane, is a type of crane used for industrial lifting and moving heavy loads within a limited range. It consists of parallel runways with a traveling bridge spanning the gap. A lifting component, known as a hoist, travels along the bridge. This setup allows the crane to move loads up and down, as well as back and forth across the room or warehouse where it is installed.
Overhead cranes are commonly found in manufacturing and industrial environments, such as factories, warehouses, and steel mills, where they are used to handle raw materials, machinery, and finished products. They are preferred for tasks that require lifting heavy or awkwardly shaped objects that might be difficult or unsafe to move by other means.
The main components of an overhead crane include:
- Bridge: The primary structural component that spans the width of the workspace. It moves along the runway beams.
- Runway: The tracks that support the bridge, allowing it to move back and forth.
- Hoist: The lifting mechanism that moves up and down, attached to the trolley.
- Trolley: The part that carries the hoist across the bridge, allowing for lateral movement.
Overhead cranes can vary greatly in terms of capacity, ranging from small workstations cranes lifting a few hundred pounds to large warehouse or shipyard cranes capable of lifting several hundred tons. They can be operated manually, electrically, or with a wireless remote, providing flexibility and precision in handling heavy loads.
What are the main types of overhead cranes?
The main types of overhead cranes are designed to meet various industrial needs, each with specific features tailored to different lifting requirements and workspace configurations. Here are the most common types:
- Single Girder Cranes: These cranes have one bridge girder supporting the trolley and hoist. They are typically used for lighter loads (up to 20 tons) and shorter spans (up to 60 feet). Single girder cranes are more cost-effective and have a simpler design, making them suitable for many small to medium lifting tasks.
- Double Girder Cranes: With two bridge girders, these cranes are designed for heavy-duty applications, capable of lifting more than 20 tons and spanning over 60 feet. Double girder cranes provide better hook height and are more durable for high-capacity lifting tasks. They are commonly used in heavy manufacturing and in places where high lift is required.
- Gantry Cranes: Gantry cranes are similar to overhead traveling cranes except that they run on a track on the floor level. The main bridge beam is supported by two legs which run on ground-level rails. Gantry cranes are used in outdoor applications like shipyards, railyards, and special project sites where overhead room may not be available.
- Jib Cranes: While not always classified strictly under overhead cranes, jib cranes offer a type of overhead lifting that consists of a horizontal beam (jib or boom) attached to a fixed location. The hoist and trolley move along the beam. Jib cranes are ideal for individual workstation applications like workshops, assembly stations, and docks.
- Bridge Cranes: This term is often used interchangeably with overhead cranes. However, it specifically refers to the configuration where the lifting mechanism (hoist) moves along a bridge. The bridge itself moves along two parallel rails mounted on either side of the facility.
- Monorail Cranes: These cranes consist of a trolley that moves along a single rail, typically mounted on the ceiling. Monorail systems are ideal for processes that require linear movement of materials and can be customized to fit various layouts, including curves and switches.
- Workstation Cranes: Designed for lighter loads (usually up to 2 tons), workstation cranes are used in smaller, more confined spaces and for precise handling. They can be either freestanding or ceiling-mounted and are often found in assembly areas, laboratories, and small machine shops.
Each type of overhead crane offers unique advantages and is suited to particular industrial applications, considering factors such as load capacity, span length, lifting height, and the operational environment.
How do overhead cranes work?
Overhead cranes operate on a relatively straightforward principle, involving a combination of mechanical, electrical, and often computer systems to lift and move loads horizontally across a facility. The basic working mechanism of an overhead crane can be broken down into several key components and their functions:
- Bridge: This is the main structural component that spans the width of the workspace. The bridge can move along the runway beams, allowing the crane to cover a wide area. In a double girder crane, there are two parallel beams for added strength and support, whereas a single girder crane has one.
- Runway: The runway is a set of tracks aligned on either side of the working area, mounted on the floor or supported by the structure of the building. The bridge moves along these runways, enabling the crane to access different parts of the workspace.
- Hoist: The hoist is the lifting component of the crane, which can move up and down. It is attached to a trolley, which allows it to move back and forth along the bridge. The hoist can be operated manually, electrically, or pneumatically, depending on the design and requirements of the crane.
- Trolley: The trolley carries the hoist across the length of the bridge. This movement, combined with the hoist’s vertical lift, enables the precise positioning of loads anywhere within the crane’s coverage area.
- Controls: Overhead cranes can be controlled from a stationary control panel, a handheld remote, or a cabin attached to the crane (for larger models). Modern cranes can also incorporate computer-based control systems that allow for automated movement and load management.
- Electrical System: For electrically powered cranes, the electrical system provides power to the motors that drive the hoist, trolley, and bridge movements. This system includes cables, power rails, or festoons to supply continuous power as the crane moves.
- Safety Devices: Overhead cranes are equipped with various safety devices to prevent accidents and ensure safe operation. These may include limit switches that stop the crane from exceeding its designed range of motion, load sensors to prevent overloading, and emergency stop buttons.
The operation of an overhead crane involves moving the crane to the desired location above the load, lowering the hoist to attach the load using a lifting attachment (like hooks, magnets, or clamps), lifting the load, transporting it to its new location, and finally lowering and releasing it. The precise control and versatility of overhead cranes make them indispensable in many industrial settings for efficient and safe handling of materials.
What industries commonly use overhead cranes?
Overhead cranes are indispensable in a wide range of industries, particularly those that involve the manufacturing, processing, or handling of heavy or large materials. Their ability to lift, lower, and move heavy loads with precision makes them a critical component in many sectors. Here are some of the key industries that commonly use overhead cranes:
- Manufacturing: Many manufacturing facilities use overhead cranes to handle raw materials, move parts during the production process, and lift finished products. This includes automotive, machinery, and equipment manufacturing where components can be heavy and cumbersome.
- Steel Production and Fabrication: Overhead cranes are vital in the steel industry for moving raw materials such as iron ore and coal, handling hot molten steel, and lifting heavy steel beams, plates, and coils. They are used extensively in both the production of steel and its fabrication into specific products.
- Warehousing and Logistics: High-capacity overhead cranes are used in warehouses and distribution centers for stacking heavy goods and moving them to and from transportation vehicles, such as trucks and railroad cars.
- Construction: Overhead cranes play a significant role in the construction industry, especially in precast concrete factories where large elements are manufactured and then transported to construction sites. They are also used for handling construction materials and equipment.
- Shipbuilding: The shipbuilding industry relies on very large overhead gantry cranes to lift heavy sections of ships during assembly. These cranes can lift entire sections of a ship’s hull or superstructure into place.
- Power Plants: In energy production facilities, including nuclear, hydroelectric, and thermal power plants, overhead cranes are used for maintenance operations and to handle heavy machinery or equipment.
- Paper Mills: Overhead cranes are used in paper mills to handle large rolls of paper and raw materials like wood pulp, as well as for maintenance tasks on the machinery used in the paper-making process.
- Mining: The mining industry uses overhead cranes for equipment maintenance, lifting heavy machinery, and moving mined materials.
- Railroad: Rail yards and maintenance facilities use overhead cranes to lift locomotives and rail cars for repair and maintenance.
- Aerospace: The aerospace industry uses overhead cranes for assembling aircraft, handling large components like wings and fuselages, and moving heavy loads within manufacturing facilities.
These industries benefit from the efficiency, safety, and versatility that overhead cranes provide, making them a key element in the logistics and production processes. The specific type and capacity of the crane used can vary greatly depending on the particular needs of each industry and application.
What are the main components of an overhead crane?
An overhead crane consists of several key components that work together to enable the lifting and moving of heavy loads within an industrial or manufacturing setting. The main components of an overhead crane include:
- Bridge: The bridge is the primary structural component that spans the width of the crane. It consists of one or two steel beams (single or double girder) and moves along the runway beams, carrying the trolley and hoist across the workspace.
- Runway Beams: These are the long beams that support the bridge of the crane. The runway beams are typically mounted along the sides of the facility’s walls or on floor-mounted columns. They guide the movement of the bridge back and forth within the facility.
- End Trucks: Located at either end of the bridge, end trucks house the wheels that ride on the runway beams, allowing the bridge to move. They are critical for the horizontal movement of the crane.
- Hoist: The hoist is the lifting mechanism of the crane. It raises and lowers the load using a wire rope or chain. Hoists can be powered manually, electrically, or pneumatically, and are mounted on the trolley.
- Trolley: The trolley carries the hoist across the length of the bridge. This allows for lateral movement of the load along the bridge’s span. Like the hoist, the trolley can be powered in various ways depending on the crane’s design.
- Controls: The operation of the crane is managed through a set of controls, which can be a fixed wired pendant, a wireless remote control, or an operator cabin attached to the crane. Advanced cranes may also include automated control systems for precise operation.
- Electrical System: For electrically powered components (such as the hoist, trolley, and bridge movement), the electrical system includes the motors, power supply cables, and control systems that provide and manage power.
- Safety Devices: Overhead cranes are equipped with various safety devices to prevent accidents and ensure safe operation. These can include overload indicators, limit switches to prevent the hoist from traveling beyond designed limits, emergency stop systems, and braking systems for both the hoist and the bridge.
- Bumper (Buffer): Bumpers are energy-absorbing devices located at the ends of the crane runway and sometimes on the trolley to prevent excessive impact when the motion of the crane or trolley is halted.
These components are essential for the crane’s operation, ensuring that it can safely and efficiently lift, move, and position heavy loads. The specific design and capacity of these components can vary widely depending on the crane’s intended use, the environment in which it operates, and the loads it is designed to handle.
What is the difference between a bridge crane and a gantry crane?
Bridge cranes and gantry cranes are both types of overhead cranes used for lifting and moving heavy loads in various industrial settings, but they differ significantly in their design and application. Here are the main differences between the two:
Bridge Crane
- Structure and Installation: A bridge crane, also known as an overhead crane, consists of a bridge that spans the width of the workspace and moves along a pair of runway beams fixed to the walls or supported by the ceiling of the facility. This design allows for efficient use of space underneath the crane.
- Mobility: The bridge of an overhead crane moves along the fixed runway beams, providing movement across the length and width of the building. This setup is ideal for indoor applications where the crane can utilize the existing structure of the building.
- Support System: Bridge cranes are typically mounted on elevated runways, and the building’s structure often supports these runways. This requires the building to have sufficient strength to support the crane and its loads.
- Application: They are commonly used in manufacturing and assembly facilities, where they can easily move loads over machinery, equipment, and workstations without interference from floor-level obstacles.
Gantry Crane
- Structure and Installation: A gantry crane features a bridge mounted on two or more legs that run on ground-level rails or, in some cases, on wheels. This design makes the gantry crane more versatile in terms of installation locations, including outdoor applications.
- Mobility: Gantry cranes can be either fixed in one location or equipped with wheels to move along a track or on a flat surface, offering flexibility in moving the crane itself to different work areas.
- Support System: Since gantry cranes are supported by their own legs, they do not rely on the building’s structure for support. This makes them suitable for outdoor use, such as in shipyards, freight yards, and construction sites where permanent crane installation is impractical.
- Application: Gantry cranes are ideal for outdoor applications or where building structures cannot support an overhead crane. They are frequently used in shipbuilding, container handling, and heavy fabrication industries.
In summary, the main difference between bridge and gantry cranes lies in their structure, support system, and typical applications. Bridge cranes are fixed to building structures and are ideal for indoor use where space efficiency is crucial. Gantry cranes, with their self-supporting design, offer more flexibility in location and are well-suited for outdoor or heavy-duty applications where the crane needs to be movable or where there is no suitable structure to support a bridge crane.
How are overhead cranes powered?
Overhead cranes can be powered in several ways, depending on their design, the environment in which they operate, and the specific requirements of the task they are designed to perform. The most common power sources for overhead cranes are electric, hydraulic, and manual, each with its unique advantages and applications. Here’s a closer look at each type:
Electric Power
The majority of overhead cranes are powered electrically. Electric cranes use motors to drive the hoist, trolley, and bridge motions. These motors are typically powered by the facility’s main electrical supply. Electric overhead cranes offer precise control, high lifting capacities, and efficiency in operations. They are suitable for a wide range of industrial applications, from light-duty manufacturing to heavy-duty lifting in steel mills and shipyards. The electrical system includes components such as motors, drives, controllers, and sometimes variable frequency drives (VFDs) for speed control of the hoist and bridge.
Hydraulic Power
Hydraulic overhead cranes are less common but are used in specific applications where their unique capabilities are required. These cranes use hydraulic systems to move the hoist, trolley, and bridge. Hydraulic power is characterized by its ability to lift very heavy loads with smooth and controlled movements. Hydraulic cranes are typically used in applications where heavy lifting is combined with a need for precise movement, such as in aerospace and marine industries. However, the initial cost, maintenance, and operation cost of hydraulic cranes can be higher than those of electric cranes.
Manual Power
Manual overhead cranes are powered by human effort, using hand chains or levers to move the hoist and trolley and to lift or lower the load. These cranes are typically used for lighter loads and in areas where electricity is not available or where simplicity and low cost are priorities. Manual cranes are common in workshops, maintenance facilities, and light assembly areas. Despite their limited lifting capacity and slower operation, manual cranes are highly reliable and require minimal maintenance.
Pneumatic Power
Additionally, some overhead cranes are powered pneumatically, especially in environments where electrical power could pose a risk, such as in explosive atmospheres. Pneumatic cranes use compressed air to operate the hoist and trolley, offering a safe alternative in hazardous environments.
In summary, the choice of power source for an overhead crane depends on the specific needs of the operation, including the weight of the loads, the environment, and the desired level of control and speed. Electric cranes are the most common due to their versatility, control, and efficiency, while hydraulic and manual cranes serve more specialized roles.
What is the maximum lifting capacity of overhead cranes?
The maximum lifting capacity of overhead cranes can vary widely, depending on their design, the materials used in their construction, and their intended industrial application. Overhead cranes can be customized or designed to handle anything from a few kilograms to several hundred tons. Here’s a general overview:
- Small Workstation Cranes: These cranes are designed for lighter tasks and can typically lift from 250 kilograms to around 2 tons (2,000 kilograms). They are commonly used in workshops, assembly lines, and small manufacturing settings.
- Standard Industrial Cranes: The majority of overhead cranes used in manufacturing and industrial environments have lifting capacities in the range of 5 tons to around 50 tons. These cranes are versatile and meet the needs of a wide range of lifting tasks.
- Heavy-Duty Cranes: For more demanding applications, such as in steel mills, heavy fabrication shops, and shipyards, cranes can have capacities from 100 tons up to about 300 tons. These heavy-duty cranes are engineered to handle large, bulky loads such as steel coils, ship sections, and large machinery.
- Specialized Custom Cranes: In some cases, overhead cranes are specially engineered to lift even heavier loads. For example, cranes used in power plants for installing and maintaining generators or in shipyards for lifting whole ship sections can have capacities exceeding 500 tons, with some able to lift over 1,000 tons. The world’s largest overhead cranes, used in shipbuilding and heavy industrial applications, can lift loads of up to several thousand tons.
The specific lifting capacity of an overhead crane is determined by factors such as the strength of its materials, the design of its structure, the power of its hoist mechanism, and the safety factors included in its engineering. When selecting or designing an overhead crane, it’s crucial to consider not only the maximum weight of the loads to be lifted but also the crane’s operational environment, the height of lift required, and the frequency of lifting operations, as these factors can all influence the required capacity and durability of the crane.
Can overhead cranes move in multiple directions?
Yes, overhead cranes are designed to move in multiple directions to allow precise placement of loads within a workspace. The ability to maneuver in different directions is one of the key advantages of overhead cranes, enabling them to efficiently handle materials across a wide area. The movement of an overhead crane is typically categorized into three main directions:
- Hoisting (Vertical Movement): The hoist mechanism lifts and lowers the load vertically. This is the primary function of the crane, allowing it to raise materials off the ground and lower them to a desired location.
- Trolley Movement (Lateral Movement along the Bridge): The trolley, which carries the hoist and the load, moves back and forth along the length of the bridge. This lateral movement enables the crane to position the load anywhere along the bridge’s span.
- Bridge Movement (Longitudinal Movement along the Runway): The entire bridge, carrying the trolley and hoist, moves along the runway beams that are fixed to the building structure or mounted on the ground. This allows the crane to cover the length of the workspace, moving the load to different areas within the facility.
These three movements — hoisting, trolley travel, and bridge travel — enable an overhead crane to access virtually any point within the area it serves, offering significant flexibility in handling materials. The movements can be controlled manually, through wired pendant stations, wireless remotes, or even fully automated systems for precise and repeatable positioning of loads.
The design of the crane, including whether it is a single girder, double girder, gantry, or another type, can affect its movement capabilities and how it is operated. However, the fundamental ability to move loads vertically, laterally, and longitudinally is common to all types of overhead cranes, making them highly versatile tools for material handling in a variety of industrial settings.
What materials are overhead cranes typically used to lift?
Overhead cranes are versatile lifting devices used across a wide range of industries, capable of handling a diverse array of materials. The specific materials an overhead crane is used to lift can vary greatly depending on the industry and the particular needs of a facility. Here are some common materials and items that overhead cranes are typically used to lift:
- Raw Materials: In industries such as steel manufacturing and processing, overhead cranes lift raw materials like iron ore, coal, and scrap metal.
- Heavy Machinery and Equipment: Cranes are used to move heavy machinery and equipment within manufacturing plants, including presses, molds, and machine tools.
- Metal Products: This includes steel beams, sheets, bars, and other metal products in fabrication shops and warehouses.
- Building Materials: Overhead cranes handle building materials such as precast concrete, lumber, and large construction components.
- Containers and Pallets: In logistics and shipping industries, cranes lift containers, pallets, and large crates.
- Vehicles: Automotive and aerospace industries use cranes to lift components and entire vehicles or aircraft during assembly.
- Large Appliances and Equipment: For example, overhead cranes are used in the assembly of large industrial appliances, generators, and turbines.
- Chemicals and Hazardous Materials: In chemical processing plants, cranes are equipped with special attachments to safely handle drums or containers of chemicals.
- Ship Components: In shipyards, cranes lift sections of ships, engines, and other large maritime components.
- Molds and Dies: Overhead cranes handle heavy and bulky molds and dies in industries such as plastics manufacturing and metal casting.
- Artwork and Historical Artifacts: In certain specialized applications, such as museum installations or construction projects involving historic preservation, overhead cranes carefully lift and place large pieces of artwork or historical artifacts.
The type of hoist and attachments used with an overhead crane can be tailored to the specific materials being lifted. For example, lifting magnets may be used for steel products, while spreader beams might be employed to lift long or awkwardly shaped items. The versatility of overhead cranes comes from their ability to be equipped with a variety of lifting devices, such as hooks, grabs, magnets, and vacuum lifters, enabling them to securely and efficiently handle a wide range of materials.
What are the key safety features of overhead cranes?
Overhead cranes are equipped with a variety of safety features designed to protect operators, workers on the ground, and the materials being handled, as well as to prevent damage to the crane itself and the facility. These safety features are crucial for preventing accidents and ensuring the smooth operation of lifting activities. Key safety features of overhead cranes include:
- Load Limiting Devices: To prevent the crane from attempting to lift loads that exceed its capacity, which could lead to mechanical failure or structural collapse. These devices can be mechanical or electronic and automatically stop the hoist from lifting once the load exceeds a preset limit.
- Emergency Stop Buttons: Located on control panels and remote controls, these buttons allow operators to immediately stop crane operation in the event of an emergency.
- Anti-Collision Systems: For facilities with multiple cranes running on the same rails, anti-collision systems prevent cranes from coming into contact with each other, minimizing the risk of accidents.
- Warning Alarms and Lights: Audible alarms and flashing lights alert personnel in the vicinity of the crane’s operation, reducing the risk of injury to those working nearby.
- Limit Switches: These switches prevent the crane from moving beyond its designated path of travel or the hoist from lifting or lowering a load too far. Limit switches ensure the crane operates within its safe operational range.
- Brake Systems: Overhead cranes are equipped with brakes on the hoist and bridge to control and halt the movement of the crane and the load. These brakes can be mechanical, electrical, or hydraulic.
- Overload Protection: This feature prevents the crane from operating if the load exceeds the maximum rated capacity, protecting the crane from damage due to overload.
- Lockout/Tagout Capability: This allows the crane to be safely locked out of service during maintenance or when not in use, preventing accidental operation.
- Operator Training and Certification: While not a physical feature of the crane, ensuring that operators are properly trained and certified is a critical safety measure. Operators should be knowledgeable about the crane’s operation, safety features, and emergency procedures.
- Regular Maintenance and Inspections: Regularly scheduled maintenance and thorough inspections are essential to ensure that all safety features and mechanical components of the crane are in good working order. This includes checking for wear and tear, ensuring all safety devices are functional, and identifying any potential issues before they lead to accidents.
- Wireless Control Systems: These allow operators to control the crane from a safe distance, reducing the risk of injury from loads moving overhead or from being in close proximity to moving machinery.
Implementing and maintaining these safety features, along with strict adherence to safety protocols and guidelines, are vital to ensuring the safe operation of overhead cranes.
What are the standard safety regulations governing overhead cranes?
The safety regulations governing overhead cranes are designed to ensure the safe operation of these lifting devices, protect workers, and minimize the risk of accidents and injuries. These regulations can vary by country and region but generally include standards for design, manufacturing, installation, operation, inspection, maintenance, and training. In the United States, several key organizations set standards and regulations for overhead cranes:
- Occupational Safety and Health Administration (OSHA): OSHA provides regulations for overhead and gantry cranes in 29 CFR 1910.179, covering general requirements for crane components, inspections, safety devices, and operational protocols to ensure workplace safety.
- American National Standards Institute (ANSI): ANSI publishes voluntary consensus standards for a wide range of products and processes, including those relevant to overhead cranes.
- American Society of Mechanical Engineers (ASME): ASME B30 series, particularly ASME B30.2 for overhead and gantry cranes, ASME B30.11 for monorails and underhung cranes, and ASME B30.17 for overhead and gantry cranes with underhung trolley or bridge, provides standards on design, specifications, maintenance, and operation of overhead cranes.
- CMAA (Crane Manufacturers Association of America): CMAA Specification No. 70 (for top running bridge and gantry type multiple girder electric overhead traveling cranes) and No. 74 (for single girder cranes) offer guidelines for the design and specifications of overhead cranes.
These regulations and standards typically address the following areas:
- Design and Construction: Specifications for the design and construction of crane components to ensure they have the strength, durability, and reliability to safely perform lifting operations.
- Inspections and Maintenance: Requirements for regular inspections and maintenance to identify and address wear and tear or any potential safety issues before they lead to failures or accidents.
- Operator Training: Guidelines for the training and certification of crane operators to ensure they have the necessary knowledge and skills to safely operate overhead cranes.
- Safety Devices: Requirements for safety devices such as limit switches, load indicators, and emergency stop functions to prevent accidents.
- Operational Procedures: Protocols for safely operating cranes, including load handling, signaling, and movement within the facility.
Compliance with these regulations is mandatory in workplaces where overhead cranes are used. Regular audits and inspections are often conducted by regulatory bodies or internal safety officers to ensure adherence to these safety standards. Additionally, companies may adopt their own safety protocols and procedures that go beyond the minimum regulatory requirements to further enhance safety in their operations.
How can operators prevent accidents while using overhead cranes?
Preventing accidents while using overhead cranes involves a combination of proper training, adherence to safety protocols, regular maintenance, and the use of protective equipment. Here are key practices that operators and facilities can implement to enhance safety and minimize the risk of accidents:
- Operator Training and Certification
- Ensure that crane operators are properly trained and certified in crane operation, safety procedures, and emergency response. Training should include both theoretical knowledge and practical skills.
- Pre-Operational Inspections
- Conduct daily or pre-shift inspections of the crane to check for any mechanical or electrical issues, including worn-out parts, damaged wire ropes, malfunctioning controls, and safety devices. This helps identify and rectify potential hazards before operations begin.
- Regular Maintenance and Inspections
- Follow a regular maintenance schedule as per the manufacturer’s recommendations and regulatory standards. This includes periodic inspections by qualified personnel to ensure all parts of the crane are in good working condition.
- Adherence to Load Limits
- Always adhere to the crane’s rated load capacity. Overloading a crane can lead to structural failure, tipping, or dropping the load, resulting in accidents and injuries.
- Use of Safety Devices
- Ensure that all safety devices, such as load limiters, emergency stop buttons, and anti-collision systems, are functional. These devices play a critical role in preventing accidents.
- Clear Communication
- Use clear and standardized hand signals or radio communication to coordinate lifts, especially in noisy environments or when the operator’s view may be obstructed.
- Maintain a Clear Work Area
- Keep the crane’s path and work area clear of obstacles, debris, and unauthorized personnel to prevent collisions and tripping hazards.
- Secure Loads Properly
- Ensure loads are properly secured and balanced before lifting to prevent slipping, swinging, or accidental release.
- Plan Lifts
- Plan each lift carefully, considering the load’s weight, balance, and the path of movement. Avoid sudden starts and stops that could destabilize the load.
- Wear Protective Gear
- Operators and workers in the vicinity of crane operations should wear appropriate personal protective equipment (PPE), such as hard hats, safety glasses, and steel-toed boots.
- Follow Work Zone Safety Protocols
- Establish and enforce safety protocols for work zones, including barriers or designated safety zones to keep unauthorized personnel out of the crane’s operating area.
- Stay Informed on Weather Conditions
- Be cautious of operating cranes in adverse weather conditions, such as high winds, which can affect the crane’s stability and the load’s movement.
By implementing these safety measures, crane operators and facilities can significantly reduce the risk of accidents and ensure a safer working environment for everyone involved.
What training is required for overhead crane operators?
Training for overhead crane operators is crucial to ensure safe and efficient operation of the cranes, as well as to comply with regulatory standards. The specific training required can vary depending on the country, local regulations, and the type of crane, but typically includes a combination of theoretical instruction and practical hands-on experience. Here’s an overview of the essential training components for overhead crane operators:
- Basic Crane Operation
- Understanding the types of cranes and their applications.
- Familiarity with the components and controls of the crane.
- Operating procedures, including start-up, maneuvering, lifting, transferring loads, and shutdown.
- Safety Training
- Recognizing and avoiding potential hazards associated with crane operation.
- Understanding the capacity and limitations of the crane.
- Proper use of safety devices and equipment.
- Emergency procedures, including what to do in case of power failure, mechanical failure, or load drop.
- Inspection and Maintenance
- Pre-operation inspection to identify any potential issues that could affect safety or operation.
- Basic maintenance practices to ensure the crane remains in good working condition.
- Understanding when to report problems and how to document inspections and maintenance activities.
- Load Handling
- Calculating load weight and ensuring it does not exceed the crane’s rated capacity.
- Rigging techniques, including the selection and inspection of slings, chains, and other attachments.
- Signaling and communication methods for coordinating lifts with other workers.
- Regulatory and Standards Compliance
- Knowledge of local, national, and industry-specific regulations and standards related to crane operation, including those set by OSHA (Occupational Safety and Health Administration), ANSI (American National Standards Institute), and ASME (American Society of Mechanical Engineers).
- Documentation and record-keeping requirements.
- Practical Skills Assessment
- Demonstrating competence in operating the crane under various conditions and scenarios.
- Successfully completing a hands-on evaluation conducted by a qualified assessor.
- Certification
- In many jurisdictions, operators must pass a certification exam to demonstrate their knowledge and skills. The certification process may involve both written and practical tests and may need to be renewed periodically.
Continuing Education
- Operators should also participate in ongoing training and refresher courses to stay up-to-date with new technologies, safety practices, and regulatory changes.
Employers are responsible for ensuring that their crane operators receive the necessary training and are competent to operate the equipment safely. The investment in comprehensive training not only promotes safety but also enhances operational efficiency and productivity.
How often should safety inspections be performed on overhead cranes?
Safety inspections for overhead cranes are crucial to ensure the equipment remains in safe working condition and to identify potential issues before they lead to accidents or equipment failure. The frequency of safety inspections can vary based on regulations, industry standards, the crane’s usage, and environmental conditions. However, there are general guidelines and best practices:
- Daily or Pre-Shift Inspections
Operators or trained personnel should perform visual and operational checks before each use or at the beginning of each shift. These inspections typically include checking for:
- Obvious structural damage or wear.
- Proper operation of controls and brakes.
- Signs of wear in lifting mechanisms and hoist ropes or chains.
- Functionality of safety devices and limit switches.
- Any unusual noises or operation issues.
- Frequent Inspections
These are more detailed inspections and are recommended to be conducted monthly to quarterly, depending on the crane’s usage and operating environment. Frequent inspections often focus on:
- Hoist chains and end connections for wear, twist, or distortion.
- Wire rope for wear, kinking, or fraying.
- Hooks for deformation or cracks.
- All functional operating mechanisms for proper operation.
- Lubrication of moving parts and checking for any leaks.
- Periodic Inspections
Conducted annually or semi-annually, periodic inspections are thorough examinations of the crane’s components and systems. They are usually performed by specialized personnel or external inspectors and include:
- Checking the structural integrity of the crane, including girders, end trucks, and runway alignment.
- Inspection of all mechanical and electrical components.
- Load testing to verify that the crane can safely lift loads up to its rated capacity.
- Review of maintenance and operation records to ensure compliance with regulations and standards.
Regulatory and Standards Compliance
- OSHA (Occupational Safety and Health Administration) in the United States, under 29 CFR 1910.179, outlines specific requirements for overhead crane inspections, including daily, frequent, and periodic inspections.
- ANSI/ASME (American National Standards Institute/American Society of Mechanical Engineers) also provides standards (such as ASME B30.2) detailing inspection criteria for different types of cranes.
Additional Considerations
- The frequency of inspections might increase based on the crane’s age, service conditions, and past performance.
- Cranes operating in harsh conditions, such as extreme temperatures, corrosive environments, or performing high-cycle or high-capacity lifts, may require more frequent inspections.
It’s crucial for employers to establish a comprehensive inspection program that aligns with regulatory requirements, industry standards, and the specific needs of their operations. Maintaining detailed records of all inspections and corrective actions taken is also essential for compliance and safety management.
What are common safety violations involving overhead cranes?
Safety violations involving overhead cranes can lead to dangerous situations, including accidents, injuries, and even fatalities, besides legal and financial repercussions for the companies involved. Some of the most common safety violations include:
- Lack of Proper Training
Operators or maintenance personnel who lack the required training and certification can inadvertently cause accidents due to improper operation or maintenance procedures.
- Overloading the Crane
Attempting to lift loads that exceed the crane’s rated capacity is a critical safety violation that can result in mechanical failures, structural damages, or the crane tipping over.
- Inadequate Inspections and Maintenance
Failure to perform regular inspections and maintenance as per the manufacturer’s recommendations and regulatory requirements can lead to equipment failure. Common oversights include not addressing wear and tear on critical components like wire ropes, brakes, and hooks.
- Improper Rigging Practices
Using damaged slings, incorrect rigging techniques, or not securing loads properly can lead to dropped loads, causing injury or damage.
- Bypassing Safety Devices
Disabling or tampering with safety devices such as limit switches, overload indicators, or emergency stop buttons undermines the crane’s built-in safety mechanisms.
- Ignoring Load Capacity Limits
Not adhering to the crane’s load capacity and the load capacity of the facility’s structure can lead to dangerous overloading situations.
- Unsafe Working Practices
Operating a crane near power lines without proper clearances, allowing personnel to ride on loads, or lifting loads over workers are examples of unsafe practices that can lead to serious accidents.
- Poor Communication
Lack of clear communication between crane operators and ground personnel can result in miscommunication and accidents, especially in noisy environments or when the line of sight is obstructed.
- Not Using Personal Protective Equipment (PPE)
Failing to use, or improperly using, PPE like hard hats, safety glasses, and steel-toed boots increases the risk of injury.
- Failure to Follow Lockout/Tagout Procedures
Not properly securing a crane during maintenance or repair can lead to accidental operation, causing injury to maintenance staff.
Regulatory Compliance
Adhering to regulations and standards set by bodies like OSHA (Occupational Safety and Health Administration) in the United States, ANSI (American National Standards Institute), and ASME (American Society of Mechanical Engineers) is crucial to avoid these safety violations. Regular training, inspections, and a culture of safety awareness are key to preventing accidents and ensuring the safe operation of overhead cranes.
How do load limits affect crane safety?
Load limits are a critical factor in crane safety, directly affecting the stability and structural integrity of crane operations. Every crane is designed with a maximum load capacity, which is determined by the manufacturer based on the crane’s design, structure, materials, and mechanical capabilities. Adhering to these load limits is essential for several reasons:
- Preventing Structural Failure
Lifting loads heavier than the crane’s rated capacity can stress the crane’s structural components beyond their designed thresholds, leading to failure. This can result in bending or breaking of beams, snapping of wires or ropes, and damage to the hoist, which could cause the load to drop or the crane to collapse.
- Maintaining Stability
Overloading a crane can affect its balance and stability, increasing the risk of the crane tipping over. Cranes are engineered to handle specific weight distributions. Exceeding these limits can shift the center of gravity in unsafe ways.
- Ensuring Mechanical Integrity
Crane components such as the hoist, trolley, and bridge are designed to operate within specific load parameters. Overloading can lead to excessive wear, premature failure of these components, and potential breakdowns during lifting operations.
- Complying with Safety Regulations
Adhering to load limits is not just a matter of best practice; it’s a legal requirement. Regulatory bodies like OSHA in the United States, as well as international standards (e.g., ISO, ANSI/ASME), mandate compliance with specified load limits to ensure workplace safety.
- Avoiding Dynamic Loading Effects
Dynamic loading occurs when moving loads suddenly accelerate or decelerate, creating additional force beyond the static load. This can happen during lifting, swinging, or dropping loads. Operating within prescribed load limits helps minimize the impact of dynamic forces, reducing the risk of overloading.
- Protecting the Load
Overloading cranes can also damage the materials being lifted. For instance, if a load exceeds the crane’s capacity, it might be dropped, causing damage to the load itself, the crane, and potentially harming workers in the vicinity.
- Ensuring Operational Efficiency
By adhering to load limits, operations can proceed smoothly without unexpected downtime caused by equipment damage or failures. This efficiency is crucial for maintaining project timelines and reducing costs.
Implementing Load Limit Safety Measures
To ensure adherence to load limits, crane operators and personnel must be properly trained to understand and respect these limits. Load measuring systems, such as load cells and overload protection devices, should be used to prevent exceeding the crane’s capacity. Regular inspections and maintenance are also necessary to ensure that all components of the crane are in good working order and that any modifications to the crane have not affected its rated capacity.
In summary, respecting load limits is foundational to crane safety, protecting both personnel and equipment from the significant risks associated with overloading.
What emergency procedures should be in place for overhead crane operations?
Emergency procedures for overhead crane operations are crucial for ensuring the safety of operators and other personnel in the event of a malfunction, power failure, or other unforeseen incidents. These procedures should be well-documented, regularly reviewed, and practiced through drills so that everyone involved knows how to act swiftly and safely. Here are key emergency procedures and considerations for overhead crane operations:
- Emergency Stop Procedures
- Clear instructions on how to perform an emergency stop of the crane and its hoist in case of an imminent danger to personnel or equipment.
- Power Failure Response
- Procedures for safely handling a sudden power outage, including securing the load and crane, and steps to safely resume operation once power is restored.
- Load Drop or Failure
- Steps to take if the crane’s load is dropped unexpectedly or if there’s a failure in the lifting mechanism, including evacuation procedures and securing the area.
- Fire and Explosion
- Guidelines on what to do in case of a fire or explosion near or involving the crane, including shutting down operations, activating fire suppression systems (if available), and evacuating the area.
- Mechanical or Electrical Malfunction
- Procedures for responding to mechanical or electrical malfunctions, including reporting the incident, isolating the crane, and steps for safe repair or inspection.
- Evacuation Plans
- Clear evacuation routes and assembly points for crane operators and all personnel in the crane operation area.
- Rescue Operations
- In case someone is injured or trapped by the crane or its load, have a plan for safe rescue operations, including the involvement of trained rescue personnel.
- Communication
- Ensure effective communication systems are in place for reporting emergencies and coordinating responses, including alarms, public address systems, and portable radios.
- First Aid and Medical Emergency
- Access to first aid kits and trained first aid personnel, as well as procedures for handling serious injuries requiring medical attention.
- Training on Emergency Procedures
- Regular training for all crane operators and ground personnel on emergency procedures, including drills to practice responding to different types of emergencies.
- Incident Reporting and Investigation
- Procedures for reporting emergencies and incidents, followed by thorough investigations to determine causes and implement corrective actions to prevent recurrence.
- Equipment Shutdown and Isolation
- Steps for safely shutting down and isolating the crane until it can be inspected or repaired by qualified personnel.
- Emergency Contact Information
- Maintain a list of emergency contact numbers, including local emergency services, maintenance personnel, and crane service providers.
Having these emergency procedures in place and ensuring they are well communicated and understood by all involved personnel are critical for minimizing the risk of injuries and damage during crane operations. Regular reviews and updates of these procedures, as well as continuous safety training, are essential components of a comprehensive safety management system.
What personal protective equipment (PPE) is required for operating overhead cranes?
The use of Personal Protective Equipment (PPE) is essential for ensuring the safety of personnel involved in overhead crane operations. The specific PPE required can vary depending on the job, the environment in which the crane is operated, and local regulations. However, there are common types of PPE that are generally recommended or required for crane operators and others working in the vicinity of crane operations:
- Hard Hats
- Protect against head injuries from falling objects, impacts, or accidental contact with electrical hazards.
- Safety Glasses or Goggles
- Shield the eyes from flying debris, dust, sparks, and other potential hazards. Goggles provide a higher level of protection, including sealing around the eyes, which is especially important in environments with high dust or particulate matter.
- Hearing Protection
- Earplugs or earmuffs to protect against hearing damage in areas with high noise levels, such as those found in many industrial environments where cranes are operated.
- Safety Shoes or Boots
- Footwear with steel toes and puncture-resistant soles to protect feet from falling objects, crushing, or puncture wounds. Some environments may also require slip-resistant soles to prevent falls.
- High-Visibility Clothing
- Vests, jackets, or other clothing with reflective material to ensure that crane operators and other personnel are clearly visible, particularly in areas with vehicle traffic or in low-light conditions.
- Hand Protection
- Gloves suitable for the specific task and environment. This could include gloves with cut resistance, vibration reduction, thermal protection, or chemical resistance, depending on the hazards present.
- Fall Protection
- For jobs that require working at heights, such as performing maintenance on the crane, harnesses, and lanyards or other fall arrest systems may be necessary to prevent falls.
- Respiratory Protection
- In environments with hazardous dust, fumes, or vapors, respirators or masks may be required to protect against inhalation of harmful substances.
- Protective Clothing
- Additional protective clothing may be required for specific operations, including coveralls for protection against chemicals, sparks, or hot metals.
The requirement for and type of PPE used should be determined by a risk assessment of the crane operation and work environment. Employers are responsible for providing the necessary PPE and ensuring that it is properly used and maintained. Additionally, crane operators and personnel should receive training on the correct use of PPE, including how to wear it properly, its limitations, and the importance of regular inspection and maintenance.
How does weather affect overhead crane safety?
Weather conditions can significantly impact the safety of overhead crane operations. Adverse weather can affect the crane’s performance, the operator’s ability to control the crane safely, and increase the risk of accidents and injuries. Here are some of the ways in which different weather conditions can affect overhead crane safety:
- Wind
- High winds can sway suspended loads, making them difficult to control and increasing the risk of collisions with structures or dropping the load. For cranes operating outdoors, such as gantry cranes, wind can also exert additional force on the crane structure itself, potentially leading to structural failure if the crane is not designed to withstand such loads.
- Rain and Wet Conditions
- Rain can make crane components slippery, increasing the risk of slippage and accidents during load handling. Wet conditions can also affect electrical systems, leading to malfunctions or short circuits. Visibility can also be reduced, making it harder for the operator to see the load and the surrounding area clearly.
- Lightning
- Operating cranes during lightning storms poses a significant risk due to the potential for lightning strikes, especially for cranes that are high off the ground and may act as lightning rods. Lightning can cause electrical failures in the crane’s systems or even direct injury to personnel.
- Snow and Ice
- Snow and ice can accumulate on the crane and its components, adding extra weight and potentially exceeding the crane’s load capacity. Ice can also make surfaces slippery, increasing the risk of slips and falls for personnel. Visibility can also be significantly reduced.
- Temperature Extremes
- Extremely cold temperatures can make metal brittle, affecting the structural integrity of the crane. Hydraulic systems may also become less efficient or fail. In contrast, extremely hot temperatures can lead to overheating of mechanical and electrical components, increasing the risk of failure.
Mitigating Weather-Related Risks
To mitigate these risks, it’s important for crane operators and safety managers to:
- Monitor weather conditions closely and adjust operations accordingly, including delaying or suspending operations during severe weather.
- Follow manufacturer guidelines for operating in various weather conditions, as cranes may have specific design limits for wind speed, temperature, and other factors.
- Conduct regular maintenance checks on cranes to ensure they are in good working condition and able to withstand weather-related stresses.
- Train crane operators and support personnel in recognizing and responding to weather-related hazards.
- Use wind speed indicators and other weather monitoring tools to make informed decisions about crane operations.
- Implement safety measures such as anti-slip surfaces, covers for electrical components, and visibility aids (e.g., lights and reflective markers) to reduce weather-related risks.
By taking these precautions, crane operators can help ensure the safety of crane operations in various weather conditions, protecting both personnel and equipment from the potential hazards posed by adverse weather.
What is the recommended maintenance routine for overhead cranes?
Maintaining overhead cranes is crucial for ensuring their safe and efficient operation. A well-defined maintenance routine can help prevent accidents, improve operational efficiency, and extend the lifespan of the equipment. Here’s a general recommended maintenance routine for overhead cranes:
Daily Checks
- Visual Inspection: Check for any visible signs of wear, damage, or abnormalities in the crane structure, hooks, wire ropes, or chain slings.
- Operational Test: Perform a brief operational test to ensure that lifting, lowering, and traveling functions are working smoothly.
- Safety Devices: Check all safety devices, including limit switches and emergency stop functions, to ensure they’re operational.
Weekly Checks
- Lubrication: Grease and lubricate moving parts according to the manufacturer’s recommendations.
- Wire Rope and Chain Inspection: Inspect wire ropes and chains for signs of wear, kinking, or corrosion.
- Brake Test: Check brakes for proper operation and adjust or replace worn components as necessary.
Monthly Checks
- Thorough Inspection: Conduct a more detailed inspection of all crane components, including the structure, hoist, and electrical systems.
- Load Test: Conduct a load test to verify that the crane can safely lift loads up to its rated capacity.
Quarterly Checks
- Electrical Systems: Inspect electrical components, including motors, controllers, and wiring, for signs of wear or damage.
- Structural Inspection: Examine the crane’s structural integrity, looking for cracks, deformation, or other signs of stress.
Semi-Annual Checks
- Full Functional Test: Perform a comprehensive operational test of all crane functions, including lifting, lowering, and horizontal movement.
- Professional Inspection: Have a qualified professional conduct an in-depth inspection of the crane, focusing on mechanical, electrical, and structural components.
Annual Checks
- Certification: Depending on local regulations, overhead cranes may require annual certification by a qualified inspector or agency.
- Load Testing: Perform or verify a full load test to ensure the crane can safely operate at its rated capacity.
Additional Recommendations
- Record Keeping: Maintain a log of all maintenance, inspections, and repairs. This documentation is crucial for identifying trends and addressing issues proactively.
- Training: Ensure that operators and maintenance personnel are adequately trained on the specific models of cranes they work with.
- Manufacturer’s Guidelines: Always follow the manufacturer’s specific maintenance recommendations, as there may be model-specific requirements.
This routine is a general guideline, and maintenance needs can vary based on the crane’s usage, environment, and manufacturer’s specifications. Always consult and adhere to the crane manufacturer’s maintenance instructions and local regulations.
How often should overhead cranes be serviced?
The frequency of service for overhead cranes depends on several factors, including the crane’s usage, operating environment, manufacturer’s recommendations, and local regulations. However, there are general guidelines that can help determine how often overhead cranes should be serviced:
- Daily to Weekly Inspections
Routine checks and minor maintenance tasks, such as visual inspections, operational tests, and basic lubrication, should be performed daily or weekly, depending on the crane’s usage and the nature of the operations.
- Monthly Inspections
A more thorough inspection is recommended on a monthly basis. This should include checking for any signs of wear or damage to mechanical, electrical, and structural components.
- Quarterly to Semi-Annual Services
Every three to six months, a detailed inspection and maintenance service should be conducted. This may involve more in-depth checks on electrical systems, load-bearing structures, and mechanical parts, as well as replacing or repairing worn or damaged components.
- Annual Inspections
At least once a year, a comprehensive inspection and service should be carried out by a qualified professional. This annual service often includes load testing, full mechanical and electrical system inspections, and structural integrity assessments. The annual inspection is crucial for ensuring compliance with safety standards and regulations.
- As-Needed Servicing
In addition to scheduled maintenance, servicing may be required on an as-needed basis to address any issues that arise during operation, such as unexpected breakdowns, malfunctions, or when wear and damage are detected during routine checks.
Regulatory and Manufacturer’s Recommendations
It’s essential to follow any specific maintenance schedules and procedures recommended by the crane’s manufacturer, as these are tailored to the particular model’s design and operational capacities. Additionally, adherence to local and industry-specific safety regulations and standards, which may dictate minimum servicing frequencies and inspection criteria, is mandatory.
The goal of regular servicing is not only to comply with legal and safety requirements but also to minimize downtime, extend the lifespan of the crane, and ensure the safety of operators and other personnel. Regular maintenance helps identify potential issues before they lead to failures or accidents, promoting a safer and more efficient working environment.
What are common issues with overhead cranes?
Overhead cranes are essential for many industrial operations, but like all machinery, they can encounter a range of issues throughout their service life. Regular maintenance and inspections are critical to minimize these problems, but understanding what common issues to look for can help in early detection and prevention. Here are some of the most common issues with overhead cranes:
- Wear and Tear of Mechanical Components
- Wire Rope Degradation: Wire ropes can fray, corrode, or become kinked, affecting the crane’s lifting capability.
- Worn Sheaves and Drums: These components can wear down over time, causing the wire rope to wear out more quickly.
- Bearing and Gear Wear: Regular movement causes wear on bearings and gears, potentially leading to failures.
- Electrical Problems
- Faulty Wiring and Connections: Loose or damaged wiring can result in malfunctions in crane operation.
- Overheating Motors: Frequent use or overloading can cause motors to overheat, reducing their lifespan.
- Control System Malfunctions: Issues with the control system can lead to operational failures or erratic crane behavior.
- Structural Issues
- Cracks or Deformations: The crane’s structure can develop cracks or deformations due to overloading or accidents, compromising safety.
- Corrosion: Exposure to harsh environments can lead to corrosion, weakening the crane’s structural integrity.
- Hoist Issues
- Malfunctioning Brakes: Brakes can wear out or fail, posing a significant safety risk.
- Load Drift: Hoist drift can occur due to issues with the brake or load control, leading to uncontrolled or unintended movement of the load.
- Chain or Rope Misalignment: Improperly aligned chains or ropes can cause uneven wear or damage, affecting the crane’s lifting capacity.
- Operational Errors
- Overloading: Exceeding the crane’s rated capacity can cause immediate or cumulative structural damage.
- Improper Rigging: Incorrect rigging practices can lead to load slippage, imbalance, or accidents.
- Lack of Training: Operator errors due to insufficient training can lead to mishandling and accidents.
- Safety Device Failures
- Limit Switches Not Working: These switches prevent the crane from over-traveling, and their failure can lead to collisions or overloading.
- Malfunctioning Alarms and Indicators: Failure of alarms and warning systems to alert operators of potential hazards.
Preventive Measures
To address and prevent these common issues, regular maintenance and inspections are essential. This includes adhering to the manufacturer’s maintenance schedule, conducting routine checks, and ensuring that operators and maintenance personnel are properly trained. Implementing a comprehensive maintenance program can significantly reduce the risk of these common issues, ensuring the safety and longevity of overhead crane operations.
How can regular maintenance prevent crane breakdowns?
Regular maintenance is crucial in preventing crane breakdowns and ensuring the safe, efficient operation of overhead cranes. Through systematic inspection, servicing, and repair, maintenance programs help identify and address potential issues before they escalate into significant problems. Here’s how regular maintenance achieves this:
- Early Detection of Issues
- Regular inspections and maintenance activities help identify wear and tear, mechanical issues, or electrical faults at an early stage. This early detection allows for the timely repair or replacement of parts before they can cause a breakdown.
- Prevention of Wear and Tear
- Maintenance routines include lubrication of moving parts, adjustment of alignments, and tightening of loose components, which can significantly reduce the rate of wear and tear. This prolongation of component life helps prevent the sudden failures that lead to breakdowns.
- Ensuring Structural Integrity
- Regular checks for cracks, corrosion, or deformation in the crane’s structure can prevent catastrophic failures. Maintenance activities ensure that the crane’s structural integrity is not compromised, thereby avoiding accidents and breakdowns.
- Optimizing Mechanical Performance
- Servicing mechanical components like gears, bearings, hoists, and brakes ensures they operate within their intended specifications. This optimization of mechanical performance prevents malfunctions that could lead to operational failures.
- Maintaining Electrical System Reliability
- Electrical systems, including motors, controls, and wiring, are inspected and serviced to prevent electrical failures. Regular maintenance ensures that electrical components are functioning correctly and safely, reducing the risk of breakdowns due to electrical faults.
- Preserving Safety Functions
- Safety devices and systems, such as limit switches, overload indicators, and emergency stop buttons, are checked and tested regularly. This ensures they are operational and can perform their protective functions, preventing overloading and other unsafe conditions that could lead to breakdowns.
- Compliance with Regulations and Standards
- Regular maintenance ensures that cranes comply with local and international safety standards and regulations. Compliance helps prevent legal issues and operational shutdowns that can arise from regulatory violations.
- Extending Equipment Lifespan
- By addressing issues promptly and keeping the crane in good working condition, regular maintenance extends the equipment’s operational lifespan. This prevents the premature replacement of components or the entire crane, which can be costly.
- Reducing Downtime and Operational Costs
- Preventive maintenance minimizes unexpected downtime by scheduling service activities during non-operational periods. This planned approach to maintenance avoids the high costs associated with emergency repairs and operational interruptions.
Implementation
Implementing a comprehensive maintenance schedule based on the manufacturer’s recommendations and adapting it to the crane’s operating conditions, usage, and environment is essential. Such a program should include daily checks, periodic inspections, and annual certifications by qualified professionals.
By investing in regular maintenance, crane operators and owners can significantly reduce the likelihood of breakdowns, enhance safety, improve operational efficiency, and extend the service life of their equipment.
What should be done if a crane malfunctions during operation?
If a crane malfunctions during operation, it’s crucial to take immediate and appropriate actions to ensure the safety of all personnel and minimize damage to the crane and surrounding property. Here are the steps that should be followed:
- Cease Crane Operation
- Immediately stop using the crane. Operators should be trained to recognize the signs of malfunction (such as unusual noises, erratic movements, or warning lights) and to stop operation safely.
- Secure the Load and Crane
- If possible and safe, lower the load to the ground or a secure location to prevent any danger from falling objects. Ensure the crane is in a stable and secure condition to prevent further movement or damage.
- Evacuate the Area
- If the malfunction poses a risk of injury, ensure that all personnel evacuate the immediate area around the crane and the load. Establish a safety perimeter to keep bystanders away.
- Notify Supervisors and Safety Personnel
- Report the malfunction to supervisors, safety officers, or the appropriate personnel as per the company’s emergency protocols. Quick communication is essential for an effective response.
- Isolate the Crane
- Implement lockout/tagout procedures to ensure that the crane cannot be operated until it has been inspected and repaired. This is crucial to prevent accidental or unauthorized use.
- Assess the Situation
- Conduct a preliminary assessment to understand the nature and extent of the malfunction, without compromising safety. This assessment should be performed by competent personnel who can safely evaluate the situation.
- Document the Incident
- Record details of the malfunction and any actions taken immediately afterward. Documentation is essential for the investigation and for developing strategies to prevent future occurrences.
- Professional Inspection and Repair
- Have the crane inspected by a qualified technician or engineer who can identify the cause of the malfunction and recommend repairs. No attempts to repair the crane should be made by unqualified personnel.
- Review and Implement Corrective Actions
- Based on the findings of the inspection, implement the recommended repairs or adjustments. Review the incident to identify any operational changes or preventive measures that could avoid similar malfunctions in the future.
- Conduct a Safety Review
- Before returning the crane to operation, conduct a thorough safety review and ensure that all necessary repairs have been made and tested. This may include retraining personnel on proper crane operation and safety procedures if the malfunction was related to operational errors.
- Gradual Resumption of Operations
- Once the crane is deemed safe for use, resume operations gradually, starting with no-load or light-load tests to ensure that the crane is functioning correctly.
Importance of Training and Preparedness
Ensuring that crane operators and emergency response personnel are properly trained to handle malfunctions is crucial. Regular training sessions, emergency drills, and familiarization with safety procedures can greatly improve the response to crane malfunctions, minimizing risks to personnel and equipment.
Are there specific lubrication requirements for overhead cranes?
Yes, overhead cranes have specific lubrication requirements that are crucial for their safe and efficient operation. Proper lubrication reduces friction between moving parts, minimizes wear, and prolongs the life of mechanical components. The lubrication requirements for an overhead crane depend on its design, the environment in which it operates, and the manufacturer’s recommendations. Here are some general guidelines:
Types of Lubricants
- Greases: Used for components that require a thicker lubricant to stay in place, such as open gears, wire ropes, bearings, and wheel flanges.
- Oils: Applied to parts needing a thinner lubricant for smoother movement or parts inside a sealed system, like gearboxes and hydraulic systems.
Key Components to Lubricate
- Wire Ropes and Chains: These should be lubricated regularly to prevent corrosion and wear. The type of lubricant often depends on the operating environment and the specific application of the crane.
- Gears and Bearings: High-pressure or extreme-pressure lubricants are typically recommended to withstand the loads and prevent metal-to-metal contact.
- Hoist and Trolley Wheels: Lubrication reduces rolling resistance and wear. It’s important for the smooth operation of the crane along the beams.
- Sheaves and Drums: Proper lubrication ensures that wire ropes move smoothly over these components, reducing wear on both the ropes and the sheaves or drums.
- Swivels, Hooks, and Other Rotating Parts: These parts require regular lubrication to maintain ease of movement and to prevent seizing.
Lubrication Frequency and Procedures
- Frequency: The manufacturer’s guidelines should always be followed for the frequency of lubrication. In general, daily to monthly inspections can help determine the need for lubrication, depending on usage intensity and environmental conditions.
- Procedure: Applying lubricant correctly is as important as the frequency. Over-lubrication can attract dirt and lead to buildup, while under-lubrication leads to increased wear. Follow the manufacturer’s instructions for the correct application methods and quantities.
Environmental Considerations
- Outdoor Cranes: May require lubricants that are more resistant to water washout and offer protection against rust and corrosion.
- Indoor Cranes: Lubricants used indoors might focus more on reducing drips and leaks to prevent contamination of products or work areas.
Monitoring and Maintenance
- Regular Inspections: Regular checks can help identify lubrication needs and assess the condition of previously lubricated components.
- Record Keeping: Maintain records of lubrication schedules and any observations made during inspections to help establish effective maintenance routines.
Manufacturer’s Recommendations
- Always consult the crane manufacturer’s maintenance manual for specific lubrication requirements, including the types of lubricants recommended and the frequency of their application. Manufacturer guidelines are tailored to the design and materials used in the crane, ensuring optimal performance and longevity.
Proper lubrication is a critical component of a comprehensive maintenance program for overhead cranes, ensuring they operate smoothly, efficiently, and safely over their service life.
How to diagnose electrical problems in overhead cranes?
Diagnosing electrical problems in overhead cranes involves systematic checks and a thorough understanding of the crane’s electrical system. Electrical issues can range from simple problems, such as loose connections, to more complex issues like malfunctioning control systems. Here’s a structured approach to diagnosing electrical problems in overhead cranes:
- Safety First
- Isolate the Crane: Ensure the crane is powered off and isolated from the power source before starting any diagnostic procedures to prevent electrical shock or accidental operation.
- Use Proper PPE: Personnel should wear appropriate personal protective equipment (PPE), such as insulated gloves and eye protection.
- Visual Inspection
- Check for Visible Signs of Damage: Look for obvious signs of wear, damage, or overheating on wires, connectors, and electrical components.
- Inspect Wiring and Connections: Loose, corroded, or damaged wiring can cause intermittent or complete loss of power and function. Ensure all connections are tight and free of corrosion.
- Check Power Supply
- Voltage Levels: Use a multimeter to check for correct voltage levels at the crane’s main power supply and at various control points. Incorrect voltage can indicate problems with the power supply or transformer.
- Fuses and Circuit Breakers: Inspect fuses and circuit breakers for signs of tripping or failure. A blown fuse or tripped breaker may be a symptom of an underlying electrical issue.
- Control System
- Inspect Control Panel: Check the control panel for loose connections, signs of arcing, or damaged components.
- Functionality Tests: Test the functionality of switches, buttons, and other control devices to ensure they are operating correctly and sending signals as intended.
- Motors and Drives
- Motor Inspection: Look for signs of overheating, unusual noises, or vibrations in motors, which can indicate electrical or mechanical issues.
- Drive Performance: Check variable frequency drives (VFDs) and other motor control devices for error codes or malfunction signs. Use a multimeter to measure input and output power to diagnose potential issues.
- Sensor and Limit Switches
- Test Sensors: Verify the operation of position sensors, overload sensors, and other safety devices to ensure they are functioning correctly and not causing unnecessary stops or faults.
- Limit Switches: Ensure limit switches are correctly adjusted and functioning, as these are critical for preventing the crane from moving beyond its designed range.
- Diagnostic Tools and Software
- Use Diagnostic Tools: Many modern cranes are equipped with diagnostic interfaces that can be used to read error codes or monitor operational parameters. These tools can provide valuable insights into electrical problems.
- Software Analysis: If available, use software tools provided by the crane manufacturer to analyze operational data and identify anomalies or patterns that could indicate electrical issues.
- Consult Documentation
- Refer to Manuals: The crane’s electrical schematic diagrams and operation manuals can provide crucial information for troubleshooting. Understanding the crane’s wiring and control logic is essential for effective diagnosis.
- Seek Professional Help
- If the problem is not easily identifiable or beyond the skill set of the maintenance team, it’s important to consult with a professional electrician or an engineer specializing in overhead cranes. Complex issues, especially those related to the crane’s control system or software, may require specialized diagnostic equipment and expertise.
Documentation and Follow-Up
- Document Findings: Keep detailed records of the symptoms, diagnostic steps taken, and any repairs or adjustments made. This documentation can be invaluable for future troubleshooting and maintenance planning.
- Follow-Up: After repairs are made, monitor the crane closely to ensure the problem has been resolved and does not recur.
Diagnosing electrical problems in overhead cranes requires a methodical approach, attention to safety, and a good understanding of the crane’s electrical systems. Regular maintenance and timely diagnosis of electrical issues are key to ensuring the safe and efficient operation of overhead cranes.
What are the signs of wear and tear on overhead cranes?
Overhead cranes are subjected to rigorous use in industrial environments, leading to wear and tear over time. Recognizing the signs of wear and tear early can prevent potential failures and accidents. Here are some common signs to watch for:
- Wire Rope Deterioration
- Fraying: Strands of the wire rope becoming loose or separated.
- Corrosion: Rust or pitting on the wire rope, which can weaken its structure.
- Broken Wires: Visible broken wires within the strands or at the terminations.
- Kinking, Crushing, or Birdcaging: Deformations that could indicate mishandling or overloading.
- Worn Sheaves and Drums
- Groove Wear: Deepening or widening of the grooves in sheaves and drums that can cause improper seating of the wire rope.
- Surface Damage: Scratches or gouges that can damage the wire rope.
- Hook Deformation
- Cracks: Small cracks can form from stress or overloading.
- Throat Opening: An increase in the hook’s throat opening indicates wear or deformation.
- Latch Condition: A damaged or malfunctioning safety latch can lead to dropped loads.
- Bearing and Gear Wear
- Noise: Unusual noises such as grinding or squealing from bearings or gears.
- Vibration: Excessive vibration during operation can indicate wear or misalignment in gears and bearings.
- Oil Leakage: Leakage around gearboxes or bearings can indicate seal failures or over-wear.
- Structural Damage
- Cracks or Bends: In the crane’s beams, girders, or other structural components.
- Corrosion: Especially in critical load-bearing areas, which can compromise the crane’s structural integrity.
- Electrical System Issues
- Frequent Electrical Faults: Regularly tripping circuit breakers or blown fuses can indicate worn electrical components.
- Worn Insulation: On wiring, leading to exposed conductors and potential short circuits.
- Brake Wear
- Reduced Performance: Taking longer to stop or not holding the load securely.
- Noise: Grinding or squealing noises from the brake system.
- Control System Issues
- Erratic Operation: Unpredictable movements or responses from the crane’s control system.
- Worn Controls: Physical wear on control devices, such as buttons and joysticks, which can lead to unclear or unresponsive commands.
- End Stops and Limit Switches
- Damage or Wear: Visible wear or damage to end stops can indicate excessive force used against crane travel limits.
- Malfunctioning Limit Switches: Can lead to over-travel, posing a risk of collision or structural stress.
Monitoring and Maintenance
Regular inspections and maintenance are crucial to identify these signs of wear and tear early. A comprehensive maintenance program should include:
- Routine Inspections: Regularly scheduled checks by qualified personnel to identify and address wear and tear.
- Preventive Maintenance: Scheduled maintenance tasks based on the manufacturer’s recommendations and usage patterns.
- Corrective Actions: Prompt repair or replacement of worn or damaged components to restore safe operation.
By paying close attention to these signs and adhering to a strict maintenance regimen, the lifespan of an overhead crane can be extended, and the safety of operations can be significantly enhanced.
How to ensure the longevity of overhead cranes through maintenance?
Ensuring the longevity of overhead cranes is critical for industrial operations, both from a safety and economic standpoint. A well-maintained crane can operate efficiently for many years. Here are key strategies for extending the life of overhead cranes through maintenance:
- Adhere to a Regular Maintenance Schedule
- Preventive Maintenance: Follow the manufacturer’s recommended maintenance schedule. This typically includes daily, weekly, monthly, and annual tasks tailored to the crane’s specific needs and operating conditions.
- Condition-Based Maintenance: Beyond routine schedules, use condition monitoring tools and techniques to address maintenance needs based on the actual condition of the crane components.
- Conduct Regular Inspections
- Daily Inspections: Operators should perform visual and operational checks for signs of wear or damage before each shift.
- Periodic Professional Inspections: Have qualified personnel conduct thorough inspections at intervals recommended by the manufacturer or required by regulations. This should include checks for structural integrity, mechanical and electrical systems, and safety devices.
- Implement Corrective Maintenance Promptly
- Address issues identified during inspections immediately to prevent them from escalating into major problems. Delaying repairs can lead to more extensive damage, higher repair costs, and increased downtime.
- Maintain Detailed Maintenance Records
- Keep comprehensive records of all maintenance and repair activities, inspections, and any incidents or malfunctions. These records can help identify trends, predict wear, and tailor maintenance practices to the crane’s specific needs.
- Use Quality Parts and Lubricants
- Always use high-quality replacement parts and lubricants specified by the crane manufacturer. Inferior quality materials can lead to premature failure and potentially unsafe conditions.
- Ensure Proper Lubrication
- Regularly lubricate moving parts to reduce friction, wear, and overheating. Follow the manufacturer’s recommendations for lubrication intervals and types of lubricants to use.
- Train Operators and Maintenance Personnel
- Ensure that operators are properly trained in the safe and efficient use of the crane. Maintenance personnel should also be trained in specific maintenance procedures and safety practices. Knowledgeable staff can prevent accidents and identify issues early.
- Monitor and Adjust for Environmental Conditions
- Consider the crane’s operating environment (e.g., temperature, humidity, exposure to corrosive substances) in maintenance practices. Environmental conditions can significantly impact wear rates and maintenance needs.
- Focus on Safety Devices and Systems
- Regularly test and maintain safety devices, such as limit switches, overload indicators, and emergency stop systems. These are critical for preventing accidents that could damage the crane and shorten its lifespan.
- Seek Professional Assistance When Needed
- For complex issues or specialized maintenance tasks, don’t hesitate to consult with or hire professionals. Expertise in crane maintenance can ensure that the work is done correctly and safely.
By following these maintenance strategies, companies can significantly enhance the reliability, safety, and longevity of their overhead cranes. Investing in maintenance not only extends the life of the equipment but also ensures operational efficiency and safety in the workplace.
What are the challenges in maintaining older overhead cranes?
Maintaining older overhead cranes presents unique challenges that require specialized attention and strategies to ensure their safe and efficient operation. As cranes age, they may become more susceptible to wear and breakdowns, and finding parts or support for outdated models can be difficult. Here are some of the primary challenges involved in maintaining older overhead cranes:
- Obsolescence of Parts and Technology
- Difficulty Finding Replacement Parts: Manufacturers may discontinue parts for older models, making it challenging to find replacements.
- Outdated Technology: Older cranes may use technology that is no longer supported, requiring upgrades or custom solutions.
- Increased Wear and Tear
- Structural Integrity: Repeated use over many years can lead to stress and fatigue in structural components, increasing the risk of cracks or failure.
- Mechanical Wear: Components such as gears, bearings, and brakes may exhibit significant wear, affecting performance and safety.
- Safety Compliance
- Meeting Modern Safety Standards: Older cranes may not meet current safety standards, necessitating modifications or upgrades to comply with regulations.
- Reliability of Safety Systems: Aging safety devices, like limit switches and overload protectors, may become less reliable, requiring careful monitoring and frequent testing.
- Documentation and Records
- Lack of Documentation: Original documentation, such as operating manuals and maintenance records, may be incomplete or missing, complicating maintenance and repair efforts.
- Historical Maintenance Practices: Inconsistent or undocumented maintenance practices over the crane’s life can lead to unforeseen issues.
- Increased Maintenance Costs
- Cost of Repairs and Upgrades: Maintaining and upgrading older equipment can be costly, especially if parts are scarce or require customization.
- Unexpected Downtime: Older cranes may experience more frequent breakdowns, leading to unplanned downtime and higher costs.
- Technical Expertise
- Finding Skilled Technicians: The knowledge and skills required to maintain older cranes may be scarce, as newer technicians may not be familiar with outdated technologies.
- Custom Solutions: Addressing the unique issues of older cranes often requires custom engineering solutions, demanding a higher level of expertise.
Strategies for Overcoming These Challenges
- Proactive Maintenance: Implement a rigorous and proactive maintenance program, focusing on regular inspections and early detection of potential issues.
- Sourcing Spare Parts: Develop relationships with suppliers who specialize in older or obsolete crane parts, or consider fabricating parts when necessary.
- Upgrading Components: Where feasible, upgrade electrical and mechanical components to modern equivalents to improve reliability and safety.
- Safety Compliance: Regularly review and update safety systems to ensure compliance with current standards, even if it means retrofitting older cranes.
- Documentation: Attempt to reconstruct or update documentation and maintenance records to assist in ongoing maintenance efforts.
- Training: Invest in training for maintenance personnel on the specifics of older crane models and technologies.
Maintaining older overhead cranes is undeniably challenging, but with careful planning, skilled maintenance, and strategic upgrades, it is possible to extend their operational life and maintain safety and efficiency standards.
What are the best practices for operating overhead cranes?
Operating overhead cranes safely and efficiently requires adherence to best practices that ensure the safety of operators and all personnel in the vicinity, as well as the protection of the load and equipment. Here are the best practices for operating overhead cranes:
- Proper Training and Certification
- Ensure all crane operators are properly trained and certified in crane operation, including understanding crane capacity, controls, and safety procedures.
- Pre-Operational Inspection
- Conduct a thorough inspection of the crane before use each day or shift, checking for any signs of wear, damage, or malfunction in the crane and its components.
- Understand Load Capacity
- Never exceed the crane’s rated load capacity. Be aware of the weight of the load and the crane’s capacity, including the capacity of slings and other rigging equipment.
- Use Correct Rigging Techniques
- Ensure that all loads are properly rigged and balanced. Use appropriate slings, chains, and hooks, and inspect them for wear or damage before use.
- Clear Communication
- Use standard hand signals or radio communication to clearly communicate with all personnel involved in the lifting operation. Establish clear communication protocols for starting, stopping, and emergency signals.
- Maintain Visibility
- The operator must have a clear view of the load and the path of travel. If the load or crane movements are obstructed, use a spotter to guide the operator.
- Control Load Movement
- Move loads smoothly and avoid sudden starts, stops, or changes of direction that could destabilize the load. Keep the load close to the ground to minimize the risk of dropping.
- Avoid Load Swing
- Take measures to prevent the load from swinging, which can cause loss of control and increase the risk of accidents.
- Keep Clear of Loads
- Ensure that all personnel stay clear of the load and the crane’s path. Never allow anyone to ride on the load or use the crane for lifting personnel unless it is specifically designed and certified for personnel lifting.
- Use Lockout/Tagout Procedures
- When the crane is not in use or requires maintenance, use lockout/tagout procedures to prevent unauthorized or accidental use.
- Follow Manufacturer’s Guidelines
- Adhere to the crane manufacturer’s operating instructions and maintenance guidelines for specific operational procedures and safety measures.
- Regular Maintenance
- Follow a regular maintenance schedule to ensure the crane is in good working condition, which helps prevent malfunctions and accidents.
- Adhere to Safety Regulations
- Comply with all applicable safety standards and regulations, including those set by OSHA (Occupational Safety and Health Administration) or equivalent authorities in your jurisdiction.
- Emergency Preparedness
- Be prepared for emergencies by knowing how to quickly lower the load and shut off the crane, and be familiar with the location and operation of emergency stop buttons.
Adopting these best practices can significantly reduce the risk of accidents and injuries, enhance operational efficiency, and extend the service life of the crane. Safety should always be the top priority in all crane operations.
How can operators increase efficiency when using overhead cranes?
Increasing efficiency in overhead crane operations not only boosts productivity but also enhances safety and extends the lifespan of the crane. Here are strategies operators can implement to achieve greater efficiency:
- Thorough Training and Certification
- Ensure operators are thoroughly trained and certified, understanding both the crane’s capabilities and its control systems. Well-trained operators can perform tasks more quickly and safely.
- Pre-Operational Planning
- Plan lifts before execution, including route, placement, and any potential obstacles. Pre-planning helps avoid delays and ensures smooth operation.
- Regular Maintenance and Inspections
- Adhere to a strict maintenance schedule to prevent downtime caused by mechanical failures. Regular inspections help identify and fix issues before they impact efficiency.
- Optimize Load Handling Techniques
- Use appropriate rigging methods and ensure loads are properly balanced. Efficient load handling reduces the time taken per lift and minimizes the risk of accidents.
- Effective Communication
- Utilize clear and effective communication methods among all team members involved in crane operations. Use hand signals, radios, or other communication devices to ensure instructions are clearly understood.
- Utilize Technology and Automation
- Implementing advanced technologies, such as anti-sway control systems, can help in making crane operations more efficient by reducing load sway and improving positioning accuracy.
- Streamline Work Processes
- Analyze and streamline work processes to reduce unnecessary movements. Organizing the workspace so that materials are easily accessible can significantly cut down on operation time.
- Implement Job Rotation and Breaks
- Rotating tasks among operators can prevent fatigue and maintain high levels of concentration, thereby increasing overall efficiency.
- Continuous Improvement Programs
- Engage in continuous improvement programs that encourage feedback from operators on challenges and inefficiencies in current operations. Implementing changes based on operator feedback can lead to significant efficiency gains.
- Safety First
- Prioritize safety to prevent accidents and unplanned downtime. Efficient operations must never compromise the safety of operators or other personnel.
- Regularly Update Operating Procedures
- As technologies and work environments evolve, regularly review and update operating procedures to include best practices and new safety standards.
- Leverage Data and Analytics
- Use data collection and analysis tools to track performance and identify areas for improvement. Metrics can include operation times, frequency of use, and maintenance records to optimize usage patterns and maintenance schedules.
- Invest in Quality Equipment
- Investing in high-quality slings, rigging hardware, and other accessories can improve the reliability and speed of crane operations.
- Environmental Considerations
- Adjust operations based on environmental conditions. For example, in outdoor operations, plan lifts based on weather conditions to avoid delays.
By focusing on these strategies, operators can significantly enhance the efficiency of overhead crane operations. Efficiency gains not only improve productivity but also contribute to a safer, more reliable, and cost-effective operation.
What is the role of load testing in crane operation?
Load testing plays a crucial role in crane operation, serving as a critical component of the overall safety and maintenance program for any lifting equipment. It is an essential process designed to ensure that overhead cranes and hoists can safely lift and move the maximum rated load as specified by the manufacturer. Here’s an overview of the role and importance of load testing in crane operation:
- Verification of Structural Integrity and Performance
- Load testing helps verify the structural integrity of the crane, ensuring that all components, including the hoist, trolley, and bridge, can handle the maximum rated load without any issues. It assesses the performance of the crane under actual operating conditions.
- Compliance with Safety Standards and Regulations
- Many jurisdictions and safety standards, such as OSHA (Occupational Safety and Health Administration) in the United States, require load testing before a new or altered crane is put into service and periodically thereafter. This ensures compliance with regulations designed to protect worker safety.
- Identification of Potential Issues
- During a load test, potential problems such as mechanical or electrical issues, structural weaknesses, and inadequate performance of lifting mechanisms can be identified. This allows for corrective actions to be taken before the crane is used in regular operations.
- Certification and Documentation
- Load testing provides documented evidence that a crane is capable of performing to its rated capacity. This documentation is crucial for regulatory compliance and can be essential for insurance purposes and in the event of an accident investigation.
- Operator Training and Familiarization
- The process of load testing can also serve as a valuable training opportunity for crane operators and maintenance personnel, allowing them to become familiar with the crane’s operation and to recognize its limits.
- Ensuring Reliability
- By confirming that the crane can operate safely at its maximum capacity, load testing ensures the reliability of the crane during normal operations. This helps prevent overloading and reduces the risk of accidents.
- Maintenance and Repair Validation
- After any significant repairs or modifications to the crane, load testing can validate the effectiveness of the maintenance work and ensure that the crane still operates safely at its rated capacity.
Load Testing Procedures
The process of load testing typically involves attaching a test load (usually 100% to 125% of the crane’s rated capacity) to the crane and then lifting, moving, and lowering the load according to a predefined procedure to simulate normal operating conditions. It’s essential that this testing is planned and conducted under the supervision of qualified personnel and in accordance with manufacturer guidelines and local regulations.
Load testing is a non-negotiable aspect of crane operation, integral to ensuring that lifting equipment is safe and reliable. By rigorously testing cranes before they enter service and after any significant alterations or repairs, organizations can safeguard their operations against accidents and ensure compliance with relevant safety standards and regulations.
How to properly secure loads for lifting?
Securing loads properly before lifting with an overhead crane is crucial for ensuring safety, preventing damage to the load, and protecting the lifting equipment and personnel involved in the operation. Here’s a comprehensive guide on how to properly secure loads for lifting:
- Understand the Load
- Assess the Weight: Ensure the weight of the load is within the crane’s lifting capacity.
- Determine the Center of Gravity: Understanding the load’s center of gravity is crucial for balancing it during lifting.
- Inspect the Load: Check for any loose parts, damages, or other conditions that might affect safe lifting.
- Choose the Right Lifting Gear
- Select Appropriate Slings: Choose slings (chain, wire rope, synthetic, etc.) based on the type, size, and weight of the load, as well as the lifting environment.
- Use Correct Rigging Hardware: Shackles, hooks, and other rigging hardware should be selected based on their capacity and compatibility with both the load and the lifting equipment.
- Use Correct Rigging Techniques
- Rigging Configuration: Depending on the load, use single, basket, choker, or multi-leg sling configurations to balance and control the load.
- Sling Angles: Be mindful of sling angles to ensure the load is balanced and the slings are not overloaded.
- Protect Slings and Load: Use corner protectors or padding to protect slings from sharp edges on the load, and protect the load from potential damage caused by rigging.
- Attach Lifting Gear Securely
- Ensure Secure Attachment: Make sure all hooks, shackles, and other attachments are securely fastened and positioned correctly.
- Avoid Twisting and Knotting: Slings and attachments should lay flat without twists, kinks, or knots that could weaken their integrity.
- Perform a Pre-Lift Check
- Verify Rigging: Double-check the rigging arrangement to ensure the load is balanced and secure.
- Test Lift: Perform a test lift by raising the load slightly off the ground to confirm stability and balance. Adjust rigging if necessary.
- Communicate Clearly
- Use Signals: Ensure there’s clear communication between the crane operator and signal person or rigging team. Use established hand signals or radio communication for clarity.
- Lift, Move, and Lower the Load Safely
- Smooth Operation: Lift, move, and lower the load smoothly to avoid swinging or jerking, which could destabilize the load.
- Monitor the Load: Keep the load under constant supervision during lifting to quickly respond to any issues.
- Follow Safety Guidelines
- Wear Personal Protective Equipment (PPE): All personnel involved in the lifting operation should wear appropriate PPE.
- Establish a Clear Area: Ensure the lifting area is clear of unnecessary personnel and obstacles.
- Training and Competence
- Ensure all personnel involved in lifting operations are trained and competent in lifting operations, rigging techniques, and safety practices.
Securing loads properly requires careful planning, the right equipment, and competent personnel. By following these guidelines, you can ensure that lifting operations are conducted safely and efficiently, minimizing the risk of accidents and injuries.
What are the guidelines for operating cranes near people?
Operating cranes near people requires strict adherence to safety guidelines to prevent accidents and ensure the well-being of everyone involved. Here are key guidelines for operating cranes in areas where people are present:
- Establish Exclusion Zones
- Create clearly marked exclusion zones around the area where the crane is operating. Only essential personnel should be allowed within this zone, and ideally, the area should be barricaded to prevent unauthorized access.
- Use Signage and Barriers
- Employ visible signage and physical barriers to warn others of crane operations in progress. This helps keep unauthorized personnel out of potentially dangerous areas.
- Effective Communication
- Ensure clear communication between crane operators, signal persons, and ground personnel. Use radios, hand signals, or other agreed-upon methods of communication to maintain awareness of crane movements and operations.
- Implement a Spotter System
- Utilize spotters or signal persons to assist the crane operator in monitoring the lifting area, especially in tight spaces or when the operator’s view may be obstructed.
- Strictly Follow Load Handling Procedures
- Never lift, swing, or lower a load over people. Ensure that loads are securely rigged and that the crane path is planned to avoid passing over personnel.
- Ensure Operator Competence
- Crane operators should be properly trained and certified. They must be knowledgeable about crane operation safety, including the specific procedures for operating near people.
- Regular Crane Maintenance and Inspection
- Conduct regular maintenance and inspection of the crane to ensure it’s in safe working condition. This reduces the risk of mechanical failures that could endanger people nearby.
- Adhere to Load Capacity Limits
- Always adhere to the crane’s rated load capacity. Overloading can lead to loss of control and potential accidents.
- Use Personal Protective Equipment (PPE)
- Ensure that all personnel in the vicinity of crane operations wear appropriate PPE, such as hard hats, high-visibility clothing, and steel-toed boots.
- Monitor Weather Conditions
- Be cautious of operating cranes in adverse weather conditions, such as high winds or lightning, which can increase the risk of accidents.
- Conduct Safety Briefings
- Hold safety briefings for all personnel involved in or near the crane operation area. Make sure everyone understands their role and the safety precautions in place.
- Emergency Preparedness
- Have an emergency response plan in place and ensure that all personnel are familiar with it. This includes knowing how to quickly and safely shut down operations if necessary.
- Continual Safety Assessments
- Regularly assess the safety measures in place and make adjustments as necessary. Continuous improvement of safety practices is vital.
By following these guidelines, crane operations can be conducted safely even in areas where people are present. The key is to prioritize safety through planning, communication, and adherence to established safety protocols.
How to manage multiple cranes in one workspace?
Managing multiple cranes in one workspace requires careful planning, coordination, and adherence to safety protocols to prevent accidents and ensure efficient operation. Here’s a comprehensive approach to managing this complex situation:
- Risk Assessment and Planning
- Conduct a thorough risk assessment to identify potential hazards related to operating multiple cranes in proximity. Consider factors such as crane paths, load swing areas, and the possibility of cranes crossing paths.
- Develop a detailed plan that includes crane operation schedules, paths, and areas of operation to minimize overlap and interference.
- Define Areas of Operation
- Clearly delineate each crane’s operating area to prevent overlap. Use physical markers or barriers when possible to visually define these areas.
- Establish exclusion zones where no unauthorized personnel or equipment can enter, especially beneath the crane’s path and around the load’s potential swing area.
- Scheduling and Coordination
- Schedule crane operations to minimize simultaneous movements in close proximity. When possible, operate cranes in a staggered fashion or allocate specific time slots for each crane’s operation.
- Implement a coordination system, possibly through a central control point or designated coordinator, to manage crane movements and ensure operators are aware of each other’s activities.
- Communication Systems
- Establish robust communication systems, such as two-way radios, to enable clear and constant communication between crane operators, spotters, and the coordination team.
- Use standardized communication protocols and signals to prevent misunderstandings.
- Use of Spotters
- Employ spotters or signal persons who can oversee crane operations and provide guidance to operators, especially when cranes’ paths may intersect or when visibility is compromised.
- Operator Training and Briefings
- Ensure all crane operators are fully trained not only in operating their specific crane but also in the protocols for working in a multi-crane environment.
- Conduct regular briefings for all personnel involved in crane operations to review schedules, coordination plans, and safety measures.
- Safety Protocols
- Implement strict safety protocols, including emergency stop procedures and lockout/tagout practices for all cranes.
- Regularly inspect and maintain cranes to ensure they are in safe working condition, reducing the risk of malfunctions that could complicate a multi-crane operation.
- Technology and Automation
- Consider using technology solutions, such as anti-collision systems, GPS, and automated scheduling tools, to enhance safety and efficiency in managing multiple cranes.
- Compliance with Regulations
- Adhere to all relevant regulations and standards for crane operation, including those related to operating multiple cranes in close proximity.
- Regular Reviews and Adjustments
- Continuously review the effectiveness of your multi-crane management strategy and make necessary adjustments based on observed operations, feedback from personnel, and any incidents or near-misses.
By carefully managing the operation of multiple cranes in one workspace through strategic planning, communication, and adherence to safety practices, it’s possible to maintain a high level of efficiency while minimizing the risk of accidents and operational interference.
What considerations should be made for lifting oversized loads?
Lifting oversized loads with cranes involves unique challenges that require careful planning and consideration to ensure safety and efficiency. Here are key considerations to keep in mind when preparing to lift oversized loads:
- Load Assessment
- Weight and Dimensions: Accurately determine the weight and dimensions of the load to select the appropriate crane and rigging equipment. Oversized loads may require special lifting attachments or spreader bars to distribute the weight evenly.
- Center of Gravity: Identify the center of gravity to ensure the load can be balanced properly during lifting. An off-center load can lead to instability and potential accidents.
- Crane Capacity and Selection
- Ensure the crane has sufficient capacity not only for the weight of the load but also for the reach and height required to move the load safely. Consider the crane’s load chart, which may vary with boom length, radius, and other operational conditions.
- Rigging Equipment
- Select rigging equipment rated for the load’s weight and size. Use slings, shackles, and other hardware that can safely accommodate the dimensions and specific requirements of the load.
- Consider using spreader bars or lifting beams to distribute the load’s weight evenly and prevent damage.
- Lifting Plan
- Develop a comprehensive lifting plan that includes the load’s path, clearance requirements, and any obstacles in the crane’s operating area. The plan should also detail the rigging arrangement and communication protocols.
- Consider environmental conditions such as wind, which can significantly affect lifting operations, especially for large surface area loads.
- Permits and Regulations
- Check for any permits required for lifting and transporting oversized loads, especially if the operation affects public areas or roadways.
- Ensure compliance with local and national regulations regarding crane operations, load securing, and transportation.
- Safety Measures
- Establish safety measures, including securing the area around the lift, using spotters or signal persons, and implementing emergency procedures.
- Ensure all personnel involved in the lift are trained and aware of their roles and the safety precautions.
- Communication
- Maintain clear and constant communication among all team members involved in the lift. Use radios, hand signals, or other effective communication methods to coordinate the operation.
- Trial Lifts and Inspections
- Conduct trial lifts, if feasible, to verify the stability and balance of the load before proceeding with the actual lift.
- Perform thorough inspections of the crane, rigging equipment, and load securing devices before the lift.
- Transportation Considerations
- For loads that need to be transported after lifting, consider the route, transportation equipment, and any special requirements for oversized loads, such as escorts or road closures.
- Environmental Conditions
- Plan the lift considering the current and forecasted weather conditions. High winds, precipitation, and other factors can pose significant risks during lifting operations.
- Emergency Preparedness
- Have a clear plan in place for handling emergencies or unexpected situations during the lift. This includes knowing how to quickly and safely lower the load and evacuate the area if necessary.
Handling oversized loads requires meticulous preparation and attention to detail. By considering these factors and implementing thorough planning and safety measures, crane operations can safely and efficiently manage the challenges posed by oversized loads.
How does crane speed affect operation safety and efficiency?
Crane speed is a critical factor in operation safety and efficiency, influencing everything from the control of the load to the overall productivity of lifting operations. Balancing speed is essential for maintaining safety without sacrificing efficiency. Here’s how crane speed affects these aspects:
Safety Considerations
- Load Control: Higher speeds can lead to increased load sway, making it more difficult to control the load. This can pose significant safety risks, especially in tight or crowded workspaces. Controlled, slower speeds help minimize sway and improve load handling.
- Reaction Time: Faster crane speeds reduce the operator’s reaction time to unexpected events or obstacles, increasing the risk of accidents. A moderate speed allows for better response to unforeseen issues, enhancing safety.
- Mechanical Stress: Operating a crane at high speeds can put additional stress on mechanical components, leading to wear and tear. This not only increases the risk of equipment failure but can also pose safety hazards if components fail during operation.
- Precision Handling: For lifts that require high precision, such as placing components in tight spaces, slower speeds are necessary. High speeds can compromise precision, leading to potential collisions or misplacements.
Efficiency Considerations
- Cycle Times: Faster crane speeds can reduce cycle times, potentially increasing overall productivity. However, this is only beneficial up to a point where safety and precision are not compromised.
- Energy Consumption: Operating a crane at higher speeds often requires more energy, which can increase operational costs. Finding the optimal speed that balances energy consumption with productivity is key.
- Wear and Maintenance: Higher speeds result in increased wear on crane components, leading to more frequent maintenance needs and potential downtime, which can offset gains in productivity.
- Operator Fatigue: Operating a crane at high speeds for prolonged periods can lead to operator fatigue, reducing efficiency and increasing the risk of errors.
Balancing Speed for Optimal Safety and Efficiency
To optimize both safety and efficiency, crane operations should consider the following:
- Use Variable Speed Controls: Modern cranes often feature variable speed controls that allow operators to adjust speed based on the specific needs of each lift, enhancing both safety and efficiency.
- Implement Speed Limitations: Establishing speed limits for different types of operations can help ensure that crane movements remain within safe parameters.
- Operator Training: Comprehensive training programs can teach operators how to effectively balance speed with safety, emphasizing the importance of controlled movements.
- Technology and Automation: Technologies such as anti-sway controls and automated positioning systems can help mitigate the negative effects of higher speeds, allowing for safer and more efficient operation.
- Regular Maintenance: Ensuring that cranes are regularly maintained and inspected can help identify any issues that might be exacerbated by higher operating speeds.
While faster crane speeds can potentially increase operational efficiency, they must be carefully managed to ensure they do not compromise safety. By utilizing modern technology, implementing appropriate speed controls, and emphasizing operator training, it’s possible to achieve a balance that maximizes productivity while maintaining a safe working environment.
What are the communication protocols for crane operation?
Effective communication is critical in crane operations to ensure safety and efficiency. Communication protocols for crane operation involve standardized methods and signals that allow crane operators, riggers, and other ground personnel to understand each other clearly, even in noisy or visually obstructed environments. Here are the key components of communication protocols in crane operations:
- Hand Signals
- Standard hand signals are used universally for crane operations. These signals are essential for directing crane movements when verbal communication isn’t possible due to distance or noise. Operators and rigging personnel should be well-versed in these signals, which cover actions like “hoist,” “lower,” “use main hoist,” “stop,” “emergency stop,” and directional movements.
- It’s crucial that only one designated signal person communicates with the crane operator at a time to avoid confusion.
- Audible Signals
- Audible signals, such as horns or bells, are used to signal start and stop operations or to alert personnel of crane movements. The specific meanings of these signals should be agreed upon and understood by all team members.
- Audible alarms on the crane itself are also used to indicate when the crane is in motion or when certain safety features, like anti-collision systems, are activated.
- Radio Communication
- Two-way radios are a common and effective means of communication for crane operations, especially over long distances or in environments where hand signals are not visible. Clear, concise communication should be used, and protocols for radio use (such as who speaks first and how to acknowledge messages) should be established.
- Radios are particularly useful for complex lifts where constant communication is necessary or when the crane operator’s view is obstructed.
- Electronic and Visual Display Systems
- Some modern cranes are equipped with electronic display systems that can communicate important information to the operator, such as load weight, boom angle, and wind speed. These systems can also display messages or alerts from ground personnel.
- Visual aids like lights can be used to indicate crane status (e.g., green for go, red for stop) to personnel in the vicinity.
- Pre-Operation Briefings
- Conducting pre-operation briefings is a critical part of communication protocols. These meetings are used to discuss the lift plan, designate signal persons, and review any special communication needs for the operation.
- Briefings ensure that everyone involved understands their roles and the communication methods that will be used.
- Emergency Communication
- Establish clear protocols for emergency communication, including signals for immediate stop or evacuation. Ensure all personnel are familiar with these protocols.
- Training and Competency
- Regular training on communication protocols is essential for all personnel involved in crane operations. This includes understanding the use of hand signals, the operation of communication devices, and the specific communication needs of each lift.
- Competency assessments can ensure that personnel are capable of effective communication in the operational environment.
Effective communication protocols are integral to the safe and efficient operation of cranes. They require not only the implementation of standardized signals and devices but also ongoing training, clear designation of responsibilities, and thorough pre-operation planning.Top of FormBottom of Form
How to choose the right crane for a specific job?
Choosing the right crane for a specific job involves evaluating several key factors related to the job’s requirements, the environment in which the crane will operate, and the characteristics of the materials being lifted. Here’s a guide to help you select the most suitable type of crane—whether it’s an overhead crane, gantry crane, jib crane, or wire rope hoist—based on various operational needs:
- Load Characteristics
- Weight of the Load: Determine the maximum weight the crane needs to lift. Each type of crane has a different lifting capacity, with overhead and gantry cranes typically able to handle heavier loads than jib cranes or wire rope hoists.
- Size and Shape of the Load: Consider the dimensions of the load and how easily it can be rigged. Some cranes, like overhead cranes with multiple hoists or large span gantry cranes, are better suited for handling large or awkwardly shaped loads.
- Operational Environment
- Indoor vs. Outdoor: Overhead cranes are commonly used indoors, such as in manufacturing facilities, whereas gantry cranes can be utilized both indoors and outdoors. Jib cranes are versatile and can be installed in both settings depending on the workspace.
- Space Constraints: Jib cranes and wire rope hoists require minimal space, making them suitable for tight areas. Overhead and gantry cranes need more space but can cover a larger area.
- Floor Conditions and Space Utilization: Gantry cranes are ideal when you cannot install overhead support structures or when the floor can bear the crane’s weight. Overhead cranes require existing overhead structures to support the crane’s runway.
- Lifting Height
- Evaluate the vertical distance the load must be moved. Overhead cranes generally offer significant lifting height, while jib cranes and wire rope hoists might be limited by their design and installation.
- Movement and Maneuverability
- Range of Movement: Overhead and gantry cranes offer movement along multiple axes—up and down, left and right, forward and backward—making them suitable for complex operations. Jib cranes offer circular or semicircular movement, ideal for serving specific workstations.
- Travel Distance: For long travel distances, overhead and gantry cranes are more efficient. Jib cranes and wire rope hoists are better for localized lifting.
- Installation and Mobility
- Permanent vs. Temporary: Consider whether the crane needs to be a permanent fixture or if you require mobility. Gantry cranes can be mobile, and some jib cranes can be mounted on movable bases, whereas overhead cranes are typically fixed installations.
- Installation Space: Ensure the selected crane type can be accommodated within your existing infrastructure without requiring extensive modifications.
- Budget Considerations
- Include not only the initial purchase and installation costs but also long-term operating and maintenance expenses. Wire rope hoists are generally less expensive than installing a full crane system but offer limited capabilities.
- Regulatory and Safety Requirements
- Review any applicable regulations or standards for crane operation within your industry and region. Ensure the chosen crane type can meet these requirements, especially regarding load capacity, operator safety, and operational safety.
By carefully considering these factors, you can select a crane that not only meets the specific needs of your operation but also enhances safety, efficiency, and productivity. Consulting with crane manufacturers or specialists can provide additional insights and ensure that the selected crane is the best fit for your application.
What are the latest technological advancements in overhead cranes?
The overhead crane industry has seen significant technological advancements aimed at improving safety, efficiency, and operational capabilities. These innovations not only enhance the performance of the cranes but also contribute to safer and more productive work environments. Here are some of the latest technological advancements in overhead cranes:
- Smart Crane Technology
- Incorporating IoT (Internet of Things) devices and sensors into crane systems allows for real-time monitoring of crane conditions, including load weight, crane movements, and operational efficiency. This technology enables predictive maintenance by identifying potential issues before they lead to failures.
- Anti-Collision Systems
- Advanced anti-collision systems use laser scanners, GPS, and other sensor technologies to prevent cranes from coming into contact with each other or with obstacles in their path. These systems can automatically slow down or stop crane movement to avoid collisions, enhancing safety.
- Automated and Remote Control Systems
- Automation technology allows cranes to be operated remotely or even to perform certain operations autonomously. Remote operation can be facilitated through wireless controls or even from offsite locations, reducing the need for operators to be in potentially hazardous areas.
- Variable Frequency Drives (VFDs)
- VFDs control the speed of the crane’s motors with precision, allowing for smooth acceleration and deceleration. This reduces load sway and mechanical wear, improving safety and extending the life of crane components.
- Regenerative Braking Systems
- These systems capture energy released during braking and feed it back into the power system, reducing energy consumption and operational costs. This technology is especially beneficial in operations where cranes are frequently lifting and lowering loads.
- Wireless Data Communication and Telemetry
- Wireless systems enable the transmission of operational data in real time to operators, maintenance teams, and management. This allows for better tracking of crane usage, operational trends, and maintenance needs.
- Advanced Load Sensing and Management
- Load sensing technologies provide accurate information about the weight and position of the load, enabling more precise handling. Combined with advanced management software, these systems can optimize lifting operations for efficiency and safety.
- Safety Enhancements
- New safety features, such as LED warning lights, sirens, and cameras, provide operators with better visibility around the crane and the load. This is particularly useful in complex lifting environments where visibility is crucial.
- Operator Assistance Features
- Features like sway control and zone limitation assist operators in controlling the crane more effectively, reducing the risk of human error. Sway control automatically corrects for load sway, while zone limitation prevents the crane from entering predefined restricted areas.
- Customizable User Interfaces
- Modern cranes come equipped with customizable user interfaces, allowing operators to adjust settings and controls according to their preferences and the specific needs of the operation. Touchscreen panels and intuitive control systems make operation easier and more efficient.
These technological advancements are transforming the way overhead cranes operate, making them safer, more efficient, and adaptable to a wide range of industrial applications. As technology continues to evolve, we can expect further innovations that will continue to improve the capabilities and safety of overhead cranes.
How has automation impacted overhead crane operations?
Automation has significantly transformed overhead crane operations, bringing about numerous benefits and also presenting new challenges. Here’s an overview of how automation has impacted the field:
Benefits of Automation in Overhead Crane Operations
- Increased Efficiency and Productivity
- Automated cranes can operate continuously without fatigue, leading to increased productivity. They can be programmed for optimal speed and movement paths, reducing cycle times and increasing throughput.
- Enhanced Safety
- Automation minimizes the need for manual operation, reducing the risk of accidents caused by human error. Automated systems can be equipped with advanced safety features like anti-collision systems, load sway control, and precise positioning, further enhancing operational safety.
- Improved Precision and Quality
- Automated cranes provide consistent and precise movements, which is particularly beneficial in applications requiring high accuracy, such as assembly operations. This precision helps in minimizing damage to materials, thereby improving overall quality.
- Reduced Operational Costs
- By optimizing crane movements, automation can lead to significant energy savings. Additionally, the reduction in manual operation can lower labor costs and reduce the potential for costly accidents and associated insurance premiums.
- Predictive Maintenance
- Automation systems can monitor the condition of crane components in real-time, identifying potential issues before they lead to failures. This predictive maintenance approach can reduce downtime and extend the life of the equipment.
Challenges and Considerations
- Initial Investment and Implementation Costs
- The upfront cost of automating crane operations can be high, including not just the cost of the automated equipment but also the integration with existing systems and infrastructure modifications.
- Technical Complexity
- Implementing automation requires a certain level of technical expertise, both for the initial setup and ongoing operation. Finding and training staff with the necessary skills can be a challenge.
- Dependence on Technology
- While automation reduces the likelihood of human error, it introduces a dependency on technology, which can have its own set of vulnerabilities, such as system failures or cybersecurity risks.
- Job Displacement Concerns
- Automation can lead to concerns about job displacement for crane operators and other personnel. However, it also creates opportunities for new roles focused on the management, maintenance, and supervision of automated systems.
Looking Forward
As technology continues to advance, the impact of automation on overhead crane operations is likely to grow. Future developments may bring even greater levels of efficiency, safety, and flexibility. To fully realize these benefits, companies will need to address the challenges of integrating new technologies into their operations, ensuring reliable performance, and managing the transition for their workforce.
Automation represents a significant shift in how overhead cranes are operated, offering the potential to transform industrial operations by making them safer, more efficient, and more cost-effective.
What are the benefits of remote-controlled overhead cranes?
Remote-controlled overhead cranes offer several significant benefits that enhance safety, efficiency, and flexibility in various industrial settings. These advantages include:
- Enhanced Safety
- Reduced Risk of Accidents: Operating cranes remotely minimizes the need for manual operation and direct contact with loads, reducing the risk of accidents and injuries.
- Better Operator Positioning: Remote control allows operators to position themselves in the safest location, away from potential hazards and with the best vantage point for overseeing operations.
- Increased Efficiency
- Faster Operation: Remote control can lead to faster operation as the operator can move to the most efficient location to monitor and control the crane, reducing downtime between lifts.
- Multi-tasking: Operators can potentially manage multiple cranes or other tasks from a single remote position, depending on the complexity and safety requirements of the operations.
- Improved Precision
- Precise Control: Modern remote controls offer precise control over crane movements, improving the accuracy of load placement and handling.
- Reduced Load Sway: Operators have a better ability to control load sway from a distance, as they can choose the best position to monitor and adjust the crane’s movements.
- Operator Comfort and Ergonomics
- Reduced Physical Strain: Remote operation reduces the physical strain on operators, as they no longer need to climb up to crane cabins or stand for long periods in potentially uncomfortable or hazardous locations.
- Customizable Control Interfaces: Remote control systems can be tailored to suit the operator’s preferences, enhancing comfort and reducing fatigue over long shifts.
- Operational Flexibility
- Versatile Deployment: Remote-controlled cranes can be more easily and safely operated in hazardous environments, tight spaces, or areas that are difficult to access.
- Adaptable to Various Applications: The same remote control system can often be used to operate different types of cranes, making it a versatile tool in facilities that use multiple cranes.
- Cost-Effectiveness
- Lower Operational Costs: Remote-controlled operations can reduce the need for additional personnel on the ground, lowering labor costs.
- Reduced Maintenance and Downtime: Improved precision and control can lead to less wear and tear on crane components, reducing maintenance costs and downtime.
- Easy Integration with Automation Systems
- Remote-controlled cranes can be easily integrated with other automated systems and technologies, such as sensors and software for monitoring and managing operations, paving the way for further efficiencies and advancements in crane operation.
- Quick Training and Implementation
- Training operators to use remote controls can be quicker and less costly than training for manual crane operation, especially with intuitive control interfaces.
Despite these benefits, it’s important to ensure that remote-controlled crane operations are implemented with robust safety protocols, including emergency stop mechanisms and fail-safes, to prevent accidents in case of signal loss or malfunction. As with any significant technological integration, assessing the specific needs and conditions of the operational environment is crucial to maximizing the benefits of remote-controlled overhead cranes.
How do smart sensors enhance crane safety and efficiency?
Smart sensors significantly enhance the safety and efficiency of crane operations through advanced monitoring, data analysis, and real-time feedback mechanisms. By integrating these sensors into crane systems, operators and management can achieve higher levels of operational control, preventive maintenance, and safety compliance. Here’s how smart sensors contribute to these improvements:
Enhanced Safety through Smart Sensors
- Load Monitoring: Sensors can precisely measure the weight of the load being lifted, ensuring that the crane does not exceed its maximum lifting capacity. This prevents overloading, which is a major safety hazard.
- Anti-Collision Systems: Smart sensors can detect the proximity of cranes to each other and to obstacles in their environment. By integrating these sensors with anti-collision software, cranes can automatically slow down or stop to avoid collisions.
- Sway Control: Gyroscopic and acceleration sensors can detect and measure load sway, enabling automated systems to adjust crane movements and minimize sway, reducing the risk of accidents and material damage.
- Structural Health Monitoring: Sensors placed on critical parts of the crane structure, such as beams and supports, can monitor for signs of strain or fatigue. Early detection of structural issues allows for timely maintenance or repairs, preventing potential failures.
Increased Efficiency through Smart Sensors
- Operational Optimization: By analyzing data from various sensors (e.g., load cycles, speed, and motor temperature), crane systems can optimize their operations for efficiency, reducing energy consumption and wear on components.
- Predictive Maintenance: Smart sensors can predict equipment failures before they occur by monitoring the condition of components like motors, brakes, and cables. This predictive maintenance approach reduces downtime and extends the lifespan of the crane.
- Real-time Positioning: GPS and RFID sensors can provide real-time information on the position of the crane and the load. This improves operational planning, allowing for quicker and more accurate load handling.
- Automated Reporting: Integration of sensors with crane management software enables automatic logging of operational data, such as usage hours, lift counts, and maintenance records. This facilitates compliance with safety regulations and streamlines reporting processes.
Implementation Considerations
- System Integration: For maximum benefit, smart sensors should be integrated into a cohesive system that can process and analyze data in real time, providing actionable insights to operators and management.
- Training and Adaptation: Operators and maintenance personnel may require training to effectively use and maintain sensor-equipped cranes and to interpret the data they provide.
- Cost-Benefit Analysis: While the initial cost of integrating smart sensors into crane systems can be significant, the long-term benefits of improved safety, reduced maintenance costs, and increased operational efficiency often justify the investment.
Smart sensors represent a significant advancement in crane technology, offering the potential to make crane operations safer and more efficient than ever before. As these technologies continue to evolve and become more accessible, their adoption in the crane industry is likely to increase, driving further improvements in operational safety and efficiency.
What role does data analytics play in crane maintenance?
Data analytics plays a pivotal role in transforming crane maintenance from a reactive to a proactive and predictive approach, significantly enhancing operational efficiency, safety, and the lifespan of the equipment. By leveraging the vast amounts of data collected from smart sensors, IoT devices, and other digital tools integrated into crane systems, data analytics can provide deep insights into crane performance, health, and usage patterns. Here’s how data analytics contributes to crane maintenance:
Predictive Maintenance
- Condition Monitoring: Data analytics tools analyze real-time data from sensors monitoring various crane components (motors, brakes, cables, etc.) to assess their condition. By identifying patterns or anomalies that may indicate wear or impending failure, maintenance can be scheduled before a breakdown occurs, reducing downtime and repair costs.
- Trend Analysis: Analyzing long-term data trends helps predict when parts are likely to fail or require service, allowing for maintenance scheduling during non-critical operation times, thereby minimizing operational disruptions.
Enhanced Safety
- Safety Compliance Monitoring: Analytics can track compliance with safety standards and operational guidelines, ensuring that cranes are operated within their safe working limits. This helps in identifying and rectifying potentially unsafe practices or conditions.
- Incident Analysis: In the event of a failure or accident, data analytics can help analyze what went wrong by looking into historical operational data leading up to the incident, contributing to future prevention strategies.
Operational Efficiency
- Usage Optimization: By analyzing data on crane usage patterns, organizations can optimize their fleet management, ensuring that cranes are utilized efficiently and reducing the need for unnecessary additional equipment.
- Energy Efficiency: Data analytics can identify opportunities to save energy based on patterns of use, such as optimizing lifting paths and speeds, leading to cost savings and environmental benefits.
Cost Reduction
- Lifecycle Management: Analytics provides insights into the lifecycle of crane components, helping companies plan for replacements or upgrades at the optimal time to balance cost and performance.
- Inventory Management: Predictive maintenance informed by data analytics reduces the need for keeping a large inventory of spare parts, as parts can be ordered just in time for scheduled maintenance.
Implementation Strategies
- Integration with Maintenance Systems: For maximum impact, data analytics should be integrated with computerized maintenance management systems (CMMS) or enterprise asset management (EAM) systems, enabling automated scheduling of maintenance tasks based on analytics insights.
- Training and Skills Development: Maintenance personnel may require training in data analysis techniques and tools to effectively interpret and act on the insights provided by analytics.
Future Trends
- Machine Learning and AI: The future of crane maintenance will likely see increased use of machine learning algorithms and artificial intelligence (AI) to further refine predictive maintenance capabilities, enabling even more precise predictions of equipment failure and maintenance needs.
Data analytics transforms crane maintenance by leveraging data to make informed decisions, ultimately improving reliability, safety, and cost-efficiency. As technology advances, the role of data analytics in crane maintenance is expected to grow, further enhancing the capabilities and benefits of smart crane operations.
How are virtual reality (VR) and augmented reality (AR) used in crane training?
Virtual Reality (VR) and Augmented Reality (AR) are increasingly being used in overhead crane training programs due to their ability to provide immersive, realistic, and safe training environments. Here’s how both technologies are applied:
Virtual Reality (VR) in Overhead Crane Training
- Simulated Training Environment: VR creates a fully immersive 3D environment where trainees can practice operating overhead cranes. This simulation includes the crane’s controls, load dynamics, and the working area, allowing for a realistic training experience without the risks associated with physical cranes.
- Risk-Free Learning: Trainees can experience a wide range of scenarios, including those that might be dangerous or impractical to recreate in real life, such as operating in extreme weather conditions or dealing with equipment failures.
- Skill Development and Assessment: VR can track the trainee’s movements, decisions, and reaction times, providing immediate feedback and allowing for the assessment of skills in a controlled setting. This helps in identifying areas of improvement and tailoring the training accordingly.
- Cost-Effectiveness: Although the initial setup for VR training systems can be high, they can be more cost-effective in the long run by reducing the need for physical training materials, minimizing wear and tear on actual equipment, and allowing for training to be conducted without interrupting normal operations.
Augmented Reality (AR) in Overhead Crane Training
- Enhanced Real-World Training: Unlike VR, AR overlays digital information onto the real world. For overhead crane training, this might involve using AR glasses or devices to display information about load weight, balance, and optimal paths for moving objects.
- On-the-Job Training: AR can be used for real-time guidance during actual crane operations. For instance, it can provide visual cues and warnings to the operator, helping to prevent accidents and improve efficiency.
- Maintenance and Troubleshooting: AR can also assist in the maintenance and troubleshooting of cranes by overlaying schematic diagrams or instructional videos over the actual equipment, guiding the trainee through the process.
Combining VR and AR for Comprehensive Training
Together, VR and AR offer a comprehensive training toolset for overhead crane operators. VR’s immersive simulations are ideal for initial training and skill development in a risk-free environment, while AR’s real-world enhancements can provide ongoing support, guidance, and advanced training on the job. This combination can significantly enhance the learning experience, reduce accidents, and improve operational efficiency.
What energy-efficient technologies are being used in overhead cranes?
Overhead cranes, essential in various industrial applications, have seen significant advancements in energy-efficient technologies. These innovations aim to reduce energy consumption, minimize environmental impact, and lower operational costs. Here are some of the key energy-efficient technologies being used in overhead cranes:
- Regenerative Braking Systems
Regenerative braking systems convert the kinetic energy generated during the crane’s lowering and braking phases into electrical energy, which can then be fed back into the power grid or used by other equipment in the facility. This not only reduces overall energy consumption but also lowers the heat generation and wear on mechanical components.
- Variable Frequency Drives (VFDs)
VFDs control the speed of the crane’s motors based on the actual load and required movement, significantly reducing energy consumption. By optimizing motor speed and reducing the occurrence of peak power consumption, VFDs ensure more efficient operation, especially during lifting, lowering, and transporting loads.
- High-efficiency Motors
The adoption of high-efficiency motors in overhead cranes reduces electrical losses and improves overall energy efficiency. These motors are designed to maintain their efficiency over a wide range of loads, making them ideal for the variable demands of crane operation.
- LED Lighting Systems
For cranes equipped with lighting, switching to LED technology can significantly reduce energy consumption. LED lights offer longer life spans, better durability, and higher efficiency compared to traditional lighting systems, thus lowering both energy and maintenance costs.
- Automated Shutdown and Power Management Systems
These systems automatically power down or enter a low-energy state when the crane is not in use for a set period. This reduces idle energy consumption, a significant factor in overall energy efficiency, especially in facilities where cranes may not be operated continuously.
- Solar Power Integration
Some facilities integrate solar panels into their crane systems, either to directly power the crane operations during daylight hours or to contribute to the facility’s overall energy needs. This sustainable energy source can offset the energy consumption of the crane operations, further reducing the environmental impact.
- Lightweight Materials
The use of high-strength, lightweight materials in crane construction reduces the energy required for crane movement and operation. By lowering the dead weight of the crane, energy efficiency is improved, especially in the lifting and moving phases.
- Advanced Control Systems
Sophisticated control systems optimize the crane’s operation by ensuring smooth acceleration and deceleration, precise load handling, and efficient path planning. This not only reduces energy consumption but also minimizes wear and tear on mechanical components.
These technologies represent a shift towards more sustainable and cost-effective operations in the material handling industry. By incorporating energy-efficient solutions, companies can significantly reduce their operational costs and environmental footprint while maintaining or improving productivity and safety standards.
How is IoT (Internet of Things) utilized in overhead crane operations?
The Internet of Things (IoT) is revolutionizing overhead crane operations by enhancing efficiency, safety, and maintenance processes. Utilizing IoT technology, cranes are equipped with sensors and connected devices that gather and transmit data in real time, allowing for smarter operation and management. Here’s how IoT is utilized in overhead crane operations:
Real-time Monitoring and Control
- Operational Data Collection: IoT sensors collect data on various parameters such as load weight, crane position, speed, and motor temperature. This information is used for real-time monitoring and optimizing crane performance.
- Remote Control and Access: Operators and managers can remotely monitor and control cranes, adjusting operations as needed from any location, which enhances flexibility and efficiency.
Predictive Maintenance
- Early Fault Detection: By continuously monitoring the condition of critical components, IoT enables the early detection of potential failures. Sensors can detect anomalies like excessive vibration, temperature changes, or wear, indicating maintenance needs before they lead to downtime.
- Maintenance Scheduling: Data collected from sensors can be analyzed to predict when maintenance should be performed, transitioning from a reactive to a proactive maintenance strategy. This helps in scheduling maintenance tasks during non-peak hours, minimizing operational disruptions.
Safety Enhancements
- Collision Avoidance: IoT technology can help in preventing collisions with other cranes, obstacles, or workers in the vicinity. Sensors can detect proximity to objects and automatically halt crane movements or alert operators to avoid accidents.
- Overload Prevention: Load sensors ensure that the crane is not exceeding its safe working load limit, reducing the risk of accidents caused by overloading.
Efficiency and Productivity Improvements
- Operation Optimization: Data analytics can be used to optimize crane operations for efficiency and productivity. By analyzing patterns and usage data, operations can be streamlined, and unnecessary movements can be minimized.
- Energy Management: IoT can also be used to monitor and manage energy consumption, identifying opportunities for reducing energy use and increasing overall operational efficiency.
Asset Management and Utilization
- Tracking Usage and Performance: IoT technology provides insights into how cranes are being used, allowing managers to make informed decisions about asset management, such as reallocating cranes to different areas based on demand or optimizing the number of cranes in operation.
- Lifecycle Management: By monitoring the crane’s usage and maintenance history, companies can better manage the lifecycle of their assets, planning for upgrades or replacements based on actual data rather than estimates.
Integration with Other Systems
- ERP and SCM Integration: IoT-enabled cranes can be integrated with Enterprise Resource Planning (ERP) and Supply Chain Management (SCM) systems, facilitating better resource planning, inventory management, and overall supply chain efficiency.
The use of IoT in overhead crane operations represents a significant shift towards digitalization in the industrial sector. By leveraging real-time data, predictive analytics, and remote capabilities, companies can achieve higher levels of safety, efficiency, and productivity in their operations.
What are the future trends in overhead crane technology?
The future trends in overhead crane technology are expected to focus on enhancing efficiency, safety, and sustainability. Innovations are being driven by advancements in digitalization, automation, and materials science. Here are some key trends likely to shape the future of overhead crane technology:
- Increased Automation and Robotics
- Autonomous Cranes: The integration of autonomous or semi-autonomous operating systems is expected to increase, allowing cranes to perform tasks with minimal human intervention, improving efficiency and reducing the risk of human error.
- Robotic Assistance: The use of robotic arms or drones in conjunction with overhead cranes for tasks like loading, unloading, and precise positioning of loads could become more common, further enhancing operational efficiency.
- Advanced IoT and Data Analytics
- Enhanced Predictive Maintenance: With more sophisticated IoT sensors and data analytics capabilities, predictive maintenance will become more accurate, helping to nearly eliminate unplanned downtime and extend equipment lifespan.
- Operational Insights: The use of big data and machine learning algorithms will provide deeper insights into operational efficiencies, load optimization, and energy management, allowing for continuous improvement of crane operations.
- Integration of Augmented Reality (AR) and Virtual Reality (VR)
- AR for Maintenance and Training: Augmented reality could provide on-the-spot information overlay for maintenance staff, showing real-time data, schematics, and step-by-step repair instructions, as well as enhancing training programs.
- VR for Simulation and Planning: Virtual reality might be used more extensively for simulating crane operations in the planning stage, allowing for better design and testing of complex lifting operations before they are carried out.
- Enhanced Safety Technologies
- Improved Collision Avoidance Systems: Future cranes could incorporate more advanced sensors and AI-driven systems for detecting and avoiding obstacles, including other cranes, structures, and personnel.
- Wearable Safety Devices: The integration of wearables that monitor the health and safety of crane operators and ground personnel could become standard, with systems in place to alert operators to potential hazards or health issues in real time.
- Energy Efficiency and Sustainability
- Electrification and Renewable Energy: The move towards electrification and the use of renewable energy sources for crane operations will continue, reducing reliance on fossil fuels and lowering carbon footprints.
- Energy Recovery Systems: Technologies that capture and reuse energy from crane operations, such as regenerative braking, will become more common, further improving the energy efficiency of crane systems.
- Lightweight and High-strength Materials
- Advanced Materials: The development of new materials with higher strength-to-weight ratios will allow for the construction of lighter, more efficient crane structures capable of handling larger loads without increasing energy consumption.
- Digital Twins and Simulation
- Digital Twins: The use of digital twins, or virtual replicas of physical cranes, will enable real-time monitoring, simulation, and analysis of crane operations, aiding in optimization and predictive maintenance.
- Customization and Modular Design
- Flexible Systems: There will be an increased focus on modular and customizable crane designs that can be easily adapted for different tasks, industries, and environments, enhancing versatility and reducing costs for users.
These trends highlight the ongoing evolution of overhead crane technology towards more automated, efficient, and safe operations, with a strong emphasis on sustainability and digital integration. As these technologies mature and become more widely adopted, they will significantly impact the efficiency and capabilities of overhead crane operations across various industries.
How can companies retrofit older overhead crane with new technology?
Retrofitting older overhead cranes with new technology is a cost-effective way for companies to extend the life of their equipment, enhance safety, improve efficiency, and meet current operational demands without the need for complete replacement. Here are steps and considerations for retrofitting older overhead cranes with new technology:
- Assessment and Planning
- Evaluate Existing Equipment: Conduct a thorough assessment of the current crane system, including its structural integrity, mechanical components, and electrical systems. Identify any areas of concern or components that are outdated.
- Determine Retrofit Objectives: Define what you aim to achieve with the retrofit, such as improving safety features, increasing lifting capacity, enhancing control precision, or reducing energy consumption.
- Consult with Experts: Engage with crane manufacturers, retrofit specialists, and engineers to ensure that the planned upgrades are feasible and will meet your operational needs.
- Technological Upgrades
- Control System Upgrades: Upgrading to a modern control system, such as variable frequency drives (VFDs) and programmable logic controllers (PLCs), can significantly improve the precision, efficiency, and safety of crane operations.
- Electrification and Power Systems: Replace outdated motors with high-efficiency ones or consider electrifying components that were previously powered by other means. Incorporate energy recovery systems where possible.
- Installation of Sensors and IoT Devices: Adding sensors for monitoring load, speed, temperature, and other critical parameters can facilitate real-time monitoring and predictive maintenance.
- Safety Enhancements: Implement updated safety systems, such as anti-collision devices, overload protection, and advanced emergency stop mechanisms.
- Structural and Mechanical Modifications
- Reinforcement or Replacement of Components: Based on the assessment, reinforce or replace structural components to handle new operational capacities or to comply with current safety standards.
- Upgrade Lifting Mechanisms: Consider replacing or upgrading hoists, trolleys, and wire ropes to increase lifting capacity, speed, and reliability.
- Digital Integration
- Data Management: Integrate digital systems for data collection and analysis to optimize operations, maintenance schedules, and energy consumption.
- Remote Monitoring and Control: Implement systems that allow for the remote monitoring and control of crane operations, enhancing flexibility and responsiveness.
- Training and Compliance
- Operator Training: Ensure that crane operators and maintenance personnel are trained on the new systems and technologies to maximize the benefits of the retrofit.
- Regulatory Compliance: Verify that the retrofit complies with all relevant standards and regulations, including safety and environmental guidelines.
- Maintenance and Support
- Maintenance Programs: Establish a maintenance program that is updated to reflect the new technologies and components installed.
- Technical Support: Secure technical support agreements with equipment suppliers or service providers to ensure ongoing support for the new systems.
Retrofitting offers a pathway to modernize older overhead cranes, making them more efficient, safer, and more adaptable to changing operational needs. By carefully planning and executing these upgrades, companies can significantly extend the operational life and value of their crane assets.
What factors affect the cost of an overhead crane?
The cost of an overhead crane is influenced by a variety of factors ranging from basic design specifications to advanced features and operational requirements. Understanding these factors can help in planning and budgeting for the acquisition or upgrade of an overhead crane system. Here are the primary factors that affect the cost:
- Type of Crane
- Bridge Cranes: Single girder versus double girder designs have different price points, with double girder cranes generally being more expensive due to their higher lifting capacity and stability.
- Gantry Cranes: The cost varies significantly based on whether it’s a full gantry, semi-gantry, or portable gantry, reflecting differences in structure and mobility.
- Jib Cranes: The cost can vary based on the type (free-standing, wall-mounted, etc.) and the reach of the arm.
- Lifting Capacity
- The maximum weight the crane is designed to lift significantly influences its cost. Higher lifting capacities require more robust designs and materials, increasing the price.
- Span Length
- The length of the crane’s span, or the distance between its supports, affects the overall structure’s complexity and the amount of material needed, thereby influencing the cost.
- Lifting Height
- The required lifting height can impact the design and cost of the crane system. Higher lifting heights might require specialized components or designs.
- Hoist Type
- The type of hoist (wire rope or chain), along with its speed and lifting capacity, can vary the cost. Wire rope hoists are generally more expensive but are suitable for heavier loads and higher duty cycles.
- Duty Cycle
- Cranes designed for higher duty cycles (more frequent lifts over a given period) require more durable components and designs, leading to higher costs.
- Quality of Components
- The quality and brand of components used (motors, brakes, controls, etc.) can significantly affect the price. Higher-quality components often offer better reliability and longevity but at a higher initial cost.
- Customization and Advanced Features
- Custom features such as variable speed controls, remote operation capabilities, anti-collision systems, and automated positioning can add to the cost. Custom designs to fit specific operational needs or facility layouts also increase the price.
- Installation and Commissioning
- The complexity of the installation process, including the need for special preparations or modifications to the existing facility, can affect the overall cost. Commissioning and testing procedures also contribute to the expense.
- Transportation and Logistics
- The cost to transport the crane components to the site and the logistics of assembling them, especially in remote or difficult-to-access locations, can impact the total cost.
- Safety and Compliance
- Adhering to national and international safety standards and regulations may require additional features or certifications, increasing the cost.
- After-sales Support and Warranty
- Extended warranties and comprehensive after-sales support services can add to the cost but provide value in terms of reduced downtime and maintenance expenses.
When planning for an overhead crane investment, it’s crucial to consider these factors in the context of the specific operational needs and long-term objectives. Working with experienced manufacturers or consultants can help in identifying the most cost-effective solution that meets the required performance and safety standards.
How to budget for an overhead crane purchase?
Budgeting for an overhead crane purchase involves careful planning and consideration of both the initial purchase price and the total cost of ownership, which includes installation, operation, maintenance, and potential downtime costs. Here are steps to create a comprehensive budget for an overhead crane purchase:
- Define Your Requirements
- Crane Type and Capacity: Determine the type of crane (e.g., bridge, gantry, jib) and the required lifting capacity based on your operational needs.
- Span and Lift Height: Identify the necessary span (distance between rails) and lift height to accommodate your facility and lifting tasks.
- Duty Cycle: Assess the frequency and type of loads to determine the duty cycle, influencing the crane’s design and cost.
- Custom Features: Consider any specialized features or customizations needed for your operations, such as variable speed controls, automation, or specific safety features.
- Estimate Initial Purchase Costs
- Acquisition Cost: Get quotes from multiple suppliers for the crane with your specified features and capacity. Include costs for any custom engineering or modifications.
- Transportation and Import Fees: If applicable, estimate the cost of shipping, including import taxes and duties for overseas manufacturers.
- Installation and Commissioning: Include estimates for professional installation, electrical work, and commissioning of the crane. This may also involve infrastructure modifications to your facility.
- Calculate Operational Costs
- Energy Consumption: Estimate the crane’s energy use based on its motor size, operational hours, and local energy rates.
- Operator Training: Budget for training your staff to safely operate the new crane, including any certification if required.
- Insurance: Consider the cost of insuring the crane against damage or liability.
- Plan for Maintenance and Repairs
- Routine Maintenance: Allocate funds for regular inspections, maintenance, and servicing to keep the crane in optimal condition.
- Repair and Spare Parts: Set aside a contingency budget for unexpected repairs or replacement parts. The availability and cost of spare parts should be considered, especially for custom or specialized equipment.
- Consider Total Cost of Ownership
- Depreciation: Account for the crane’s depreciation to understand its value over time, especially if you plan to replace or upgrade in the future.
- Resale Value: If applicable, consider the potential resale value of the crane, which can offset part of the initial investment.
- Review Financing Options
- Purchase vs. Lease: Compare the costs and benefits of purchasing the crane outright versus leasing options. Leasing can reduce upfront costs but may be more expensive in the long term.
- Financing: If financing the purchase, include the cost of interest and any finance charges in your budget.
- Include a Contingency Fund
- Unexpected Costs: It’s prudent to include a contingency of 10-20% of the total budget to cover unforeseen expenses or price fluctuations.
- Seek Expert Advice
- Consulting with industry experts, manufacturers, or an independent engineer can provide insights into optimizing your budget and ensuring you meet all your operational requirements without overspending.
Creating a detailed budget with a clear understanding of both initial and ongoing costs will help ensure that your investment in an overhead crane meets your operational needs while remaining financially sustainable.
What are the financing options for buying overhead cranes?
Financing the purchase of an overhead crane is a significant decision for many businesses, allowing them to spread out the expense over time while benefiting from the equipment immediately. Several financing options are available, each with its advantages and considerations. Here’s an overview of common financing options for buying overhead cranes:
- Equipment Loans
- How It Works: Similar to other loans, equipment loans provide you with the capital to purchase the crane, which you then pay back with interest over a predetermined period.
- Benefits: You own the equipment outright once the loan is paid off, and the crane itself often serves as collateral for the loan, potentially reducing the need for additional collateral.
- Considerations: Requires a down payment (typically 10-20% of the purchase price) and a good credit score to qualify for the best terms.
- Operating Leases
- How It Works: An operating lease allows you to use the equipment for a set term without owning it, similar to renting. At the end of the lease term, you can return the equipment, extend the lease, or sometimes purchase the equipment at market value.
- Benefits: Lower monthly payments than loans and flexibility at the end of the lease term. Payments are often considered an operating expense, which can have tax benefits.
- Considerations: Over the long term, leasing can be more expensive than purchasing if you choose to buy the equipment at the end of the lease.
- Finance Leases (Capital Leases)
- How It Works: Finance leases are similar to operating leases but are structured so that you own the equipment at the end of the lease term, either through a nominal buyout or by paying the equipment’s residual value.
- Benefits: Enables eventual ownership and the lease payments go towards the purchase of the equipment. Tax benefits include depreciation and interest expense deductions.
- Considerations: Higher monthly payments than operating leases and you’re generally responsible for maintenance and repairs.
- Equipment Finance Agreements (EFAs)
- How It Works: EFAs are a hybrid financing option that combines elements of a loan and a lease. You make regular payments over time and automatically own the equipment at the end of the term without any additional buyout fees.
- Benefits: Simple structure with the benefits of ownership, including depreciation and tax deductions.
- Considerations: May require a down payment and typically involves taking on the responsibilities of ownership from the start.
- Manufacturer or Dealer Financing
- How It Works: Many manufacturers or dealers offer financing options directly to buyers, sometimes with promotional terms like lower interest rates or deferred payments.
- Benefits: Convenient to arrange at the point of sale and may offer favorable terms as an incentive to purchase.
- Considerations: Options and terms vary widely, so it’s important to compare these offers with external financing to ensure you’re getting the best deal.
- Government Loans and Grants
- How It Works: In some regions, government programs offer loans or grants to businesses for capital investments like purchasing equipment. These programs may have favorable terms or be targeted at specific industries or business sizes.
- Benefits: Potentially lower interest rates and supportive terms designed to encourage business investment and growth.
- Considerations: May come with specific eligibility requirements or usage stipulations.
Choosing the Right Option
When selecting a financing option, consider factors such as the total cost of ownership, cash flow impact, tax implications, and your long-term business strategy. It’s also wise to consult with a financial advisor or accountant to understand the full implications of each option and how it aligns with your business’s financial health and goals.
What should buyers look for in an overhead crane vendor?
Selecting the right overhead crane vendor is crucial for ensuring you receive a high-quality product that meets your specific operational needs, along with reliable after-sales support. Here are key factors buyers should consider when choosing an overhead crane vendor:
- Experience and Reputation
- Look for vendors with a solid track record and extensive experience in designing, manufacturing, and installing overhead cranes. Experienced vendors are more likely to understand complex requirements and deliver reliable solutions.
- Research their reputation in the market by reading reviews, asking for references, and checking their portfolio of completed projects.
- Product Quality and Compliance
- Ensure the vendor provides cranes that comply with industry standards and safety regulations. High-quality materials and components extend the life of the crane and reduce maintenance costs.
- Verify that the vendor’s products are certified by relevant authorities or conform to international quality standards.
- Customization Capabilities
- Each business has unique needs based on its operations, facility layout, and lifting requirements. A good vendor should offer customization options to tailor the crane to your specific needs.
- Assess whether the vendor can provide a wide range of crane types, capacities, and features that match your requirements.
- Technical and Engineering Support
- The vendor should have a competent engineering team that can provide technical support, from the initial design phase through installation and commissioning.
- Check if they offer site visits to assess your needs and propose the most suitable crane solutions.
- After-sales Service and Support
- Reliable after-sales support is essential for maintaining crane operations and minimizing downtime. Look for vendors that offer comprehensive maintenance and repair services.
- Inquire about their availability for emergency services, spare parts availability, and the typical response time for support requests.
- Safety Features and Training
- Safety is paramount in crane operations. Ensure the vendor offers modern safety features, such as overload protection, anti-collision systems, and emergency stop functions.
- Check if the vendor provides training for your operators and maintenance personnel to ensure safe and efficient crane operation.
- Pricing and Financing Options
- While cost should not be the only consideration, it’s important to ensure that the vendor’s pricing is competitive and transparent. Ask for detailed quotes that include all costs, such as installation, training, and after-sales services.
- Some vendors may offer financing options or leasing agreements, which can help in managing the investment more effectively.
- Lead Times and Project Management
- Understand the vendor’s lead times for delivery and installation. Long delays can impact your project timelines and operational efficiency.
- Assess the vendor’s ability to manage the project effectively, ensuring that the crane is delivered and installed within the agreed timelines and budget.
- Environmental and Energy Efficiency
- If sustainability is a concern for your company, consider vendors that offer energy-efficient crane solutions and use environmentally friendly manufacturing processes.
- Partnership Approach
- Look for a vendor who views the relationship as a partnership rather than just a transaction. A good vendor will be interested in understanding your business and working with you to solve challenges over the long term.
Choosing the right overhead crane vendor involves thorough research and due diligence. By focusing on these factors, you can select a vendor that not only meets your current needs but can also support your operations as they evolve and grow.
How do custom crane solutions compare to off-the-shelf options?
Custom crane solutions and off-the-shelf crane options cater to different needs and scenarios within industries requiring overhead lifting capabilities. Here’s a comparative analysis of both to help understand which might be suitable for specific operational requirements:
Custom Crane Solutions
Advantages:
- Tailored Design: Custom cranes are designed to meet the specific requirements of your operation, including unique lifting capacities, spans, heights, and special environmental conditions. This ensures optimal efficiency and safety.
- Flexibility: They offer flexibility in design and functionality, adapting to existing structures, space limitations, or future expansion plans.
- High Efficiency: By being tailored to precise operational needs, custom cranes can enhance workflow efficiency, reduce cycle times, and improve overall productivity.
- Innovative Features: Custom solutions can incorporate the latest technology and innovative features that might not be available in standard models, such as advanced automation and intelligent monitoring systems.
Disadvantages:
- Higher Cost: Customization typically comes at a higher initial cost due to the need for specialized design, engineering, and manufacturing processes.
- Longer Lead Times: The process of designing, fabricating, and installing a custom crane takes longer than purchasing a ready-made option.
- Complexity in Maintenance: Custom cranes might require specialized maintenance and parts, potentially increasing the long-term operating costs.
Off-The-Shelf Crane Options
Advantages:
- Cost-Effectiveness: Standard cranes are generally more cost-effective due to mass production, standardization of parts, and reduced engineering time.
- Quicker Availability: With pre-designed and pre-manufactured components, off-the-shelf cranes offer shorter lead times for delivery and installation.
- Simplicity: Standard cranes are designed for general applications, making them simpler to operate and maintain. The availability of spare parts and support is typically more straightforward.
- Proven Designs: Off-the-shelf cranes are based on proven designs that have been tested and refined over time, ensuring reliability and performance.
Disadvantages:
- Limited Customization: While some level of customization might be possible, off-the-shelf cranes may not perfectly fit specific operational needs or physical constraints of a facility.
- Compromises: Businesses may need to make compromises on features, capacities, or functionalities, which could affect operational efficiency or future scalability.
- Generic Features: Standard cranes may lack the advanced features or technologies that can be integrated into custom solutions, potentially limiting performance or efficiency gains.
Making the Choice
The decision between a custom crane solution and an off-the-shelf option depends on several factors:
- Operational Requirements: Consider the specific needs of your operation, including load, reach, environment, and any unique requirements.
- Budget Constraints: Evaluate your budget not just for the initial purchase but also for long-term operational and maintenance costs.
- Timeline: Determine your timeline for needing the crane operational. If time is critical, an off-the-shelf option may be more feasible.
- Future Plans: Consider future needs and potential changes in your operation that could affect the crane’s suitability.
Custom crane solutions are ideal for businesses with specific operational needs, unique facility challenges, or those looking to maximize efficiency and productivity through tailored designs. Off-the-shelf cranes, on the other hand, offer a quick, cost-effective solution for more standardized lifting needs. The choice between the two should be based on a thorough analysis of your current and future needs, budget, and timeline.
What warranty options are available for overhead cranes?
Warranty options for overhead cranes vary by manufacturer and can significantly impact long-term maintenance costs and operational reliability. A comprehensive warranty can provide peace of mind, ensuring that any defects or issues that arise after installation are addressed without additional expense to the buyer. Here are common types of warranty options you might encounter when purchasing an overhead crane:
- Standard Manufacturer’s Warranty
- Coverage: This typically covers defects in materials and workmanship for a specified period, which can range from one to several years, depending on the manufacturer and the components of the crane.
- Limitations: There may be limitations regarding what parts are covered and under what conditions the warranty applies. For instance, wear items like wire ropes and brake linings might be excluded or have shorter coverage periods.
- Extended Warranty
- Coverage: For an additional cost, some manufacturers offer extended warranty options that prolong the coverage period beyond the standard warranty. This can include parts, labor, or both.
- Benefits: Provides longer protection against potential defects and malfunctions, reducing the risk of unforeseen repair costs.
- Comprehensive Warranty Plans
- Coverage: More inclusive warranties may cover not only defects but also include preventative maintenance services, inspections, and even wear-and-tear items over the warranty period.
- Considerations: While offering greater peace of mind, these warranties can be significantly more expensive and should be weighed against the expected maintenance costs and the operational criticality of the crane.
- Parts Warranty
- Coverage: Specifically covers replacement parts provided by the manufacturer for defects. This type of warranty is common for components that may need replacement during the life of the crane, such as motors or electronic controls.
- Details: The duration of coverage for parts can vary, and labor costs for replacement may not be included unless specified.
- Labor Warranty
- Coverage: Some warranties, particularly comprehensive or extended plans, might also cover the labor costs associated with repairing or replacing defective components under warranty.
- Importance: Labor can be a significant portion of repair costs, so this type of warranty can offer substantial savings.
- On-site Service Warranty
- Coverage: Includes on-site repair services for issues covered under warranty, ensuring that certified technicians perform repairs or maintenance.
- Advantage: Minimizes downtime by providing direct access to expert service without the need to transport the crane or its components off-site for repairs.
Evaluating Warranty Options
When considering warranty options, it’s crucial to:
- Read the Fine Print: Understand exactly what is and isn’t covered, including any conditions or maintenance requirements that must be met for the warranty to remain valid.
- Consider Operational Impact: Evaluate the warranty in the context of your operations. Frequent use or operation in harsh conditions may justify the cost of more comprehensive coverage.
- Compare Costs: Analyze the cost of additional warranty coverage against the estimated cost of maintenance and repairs over the same period.
- Negotiate: Don’t hesitate to negotiate warranty terms with the manufacturer. In some cases, you might be able to extend the coverage or include additional services at a reduced cost.
A good warranty can mitigate the financial risks associated with equipment failure and maintenance. When purchasing an overhead crane, carefully consider the warranty options available to ensure they align with your operational needs and risk management strategies.
How to calculate the total cost of ownership for an overhead crane?
Calculating the total cost of ownership (TCO) for an overhead crane involves considering all costs associated with the purchase, operation, maintenance, and eventual disposal of the crane over its expected lifespan. Understanding the TCO helps businesses make informed purchasing decisions, comparing not just the initial purchase price but the long-term financial implications. Here’s a step-by-step approach to calculating the TCO for an overhead crane:
- Initial Acquisition Cost
- Purchase Price: The upfront cost of the crane, including any customization or specific features required for your operations.
- Installation and Commissioning: Costs associated with installing the crane and getting it operational, which may include structural modifications to your facility, electrical work, and testing.
- Operation Costs
- Energy Consumption: Estimate the crane’s energy use based on its motor size, operational hours, and local energy rates. Electric cranes, for example, will have different energy costs based on usage patterns.
- Operator Training and Salaries: Costs for training crane operators and ongoing salary expenses. Efficient operation can reduce wear and tear and energy usage, impacting TCO.
- Maintenance and Repair Costs
- Routine Maintenance: Scheduled maintenance costs, including inspections, lubrication, and part replacements that are predictable and planned.
- Unscheduled Repairs: Costs for unexpected repairs or replacements due to breakdowns or failures. This can vary widely based on crane usage and operating conditions.
- Spare Parts: Costs of keeping or sourcing spare parts for maintenance and repairs.
- Downtime Costs
- Lost Productivity: The cost associated with operational downtime during maintenance, repairs, or failures. This includes lost production and potential delays in project timelines.
- Rental Costs: If a temporary crane is needed during lengthy repairs or maintenance, include the rental costs in the TCO.
- End-of-Life Costs
- Depreciation: The decrease in the crane’s value over time, which can impact the residual value if you plan to sell or trade the crane.
- Disposal or Sell-off Costs: Costs associated with dismantling and removing the crane or any proceeds from selling the crane at the end of its useful life.
- Additional Considerations
- Financing Costs: If the crane is financed, include the interest and any finance charges over the life of the loan.
- Insurance: Annual insurance costs to cover potential damage to the crane, property, or personnel.
- Tax Implications: Potential tax benefits such as depreciation deductions or investment credits that can offset some of the TCO.
Calculating TCO
To calculate the TCO, sum up all the costs associated with each of the categories over the expected lifespan of the crane:
TCO=Initial Acquisition Cost+Operation Costs+Maintenance and Repair Costs+Downtime Costs+End-of-Life Costs+Additional ConsiderationsTCO=Initial Acquisition Cost+Operation Costs+Maintenance and Repair Costs+Downtime Costs+End-of-Life Costs+Additional Considerations
Example Calculation
Let’s say the initial purchase and installation cost for a crane is $100,000. Over a 10-year expected lifespan, you estimate:
- Annual operation costs: $5,000
- Annual maintenance and repair costs: $3,000
- Downtime costs: $2,000 per year
- End-of-life disposal costs: $10,000
- Financing, insurance, and tax implications total an additional $20,000 over the lifespan.
The TCO would be calculated as follows:
TCO=$100,000+(10×($5,000+$3,000+$2,000))+$10,000+$20,000TCO=$100,000+(10×($5,000+$3,000+$2,000))+$10,000+$20,000
TCO=$100,000+$100,000+$10,000+$20,000=$230,000TCO=$100,000+$100,000+$10,000+$20,000=$230,000
This simplified example shows how to structure the calculation. The actual calculation will depend on accurate and detailed cost estimates specific to your operation and the crane in question.
What are the delivery and installation considerations for new overhead cranes?
Delivery and installation are critical phases in the acquisition of a new overhead crane, involving logistical, technical, and safety considerations. Proper planning and execution are essential to ensure the crane is installed efficiently, safely, and in compliance with all regulations and standards. Here are key considerations for the delivery and installation of new overhead cranes:
- Pre-Delivery Planning
- Site Assessment: Evaluate the installation site to identify any potential challenges such as space constraints, structural integrity for supporting the crane, and access for delivery vehicles.
- Infrastructure Modifications: Determine if modifications to the existing infrastructure (e.g., reinforcing floors, installing rail systems, or electrical upgrades) are necessary to accommodate the new crane.
- Permits and Approvals: Secure any required permits or approvals in advance of delivery, including building permits, electrical permits, or special transportation permits for oversized loads.
- Logistics and Transportation
- Transportation Mode: Plan for the most appropriate mode of transportation based on the crane’s size, weight, and the distance it needs to travel. Consider special arrangements for oversized or heavy loads.
- Delivery Schedule: Coordinate the delivery schedule with the manufacturer and any contractors involved in the installation. Ensure the site is prepared, and personnel are available to receive the equipment.
- Unloading and Staging: Arrange for the necessary equipment and personnel to safely unload the crane components upon arrival and stage them for installation.
- Installation Preparation
- Installation Team: Ensure that a qualified and experienced team is in place for the installation, including certified crane installers, electricians, and any required specialists.
- Safety Plan: Develop a comprehensive safety plan for the installation process, including risk assessments, emergency procedures, and personal protective equipment (PPE) requirements.
- Tool and Equipment Checklist: Prepare a list of all tools and equipment needed for the installation, ensuring they are on site and in good working order before starting.
- Installation Process
- Follow Manufacturer’s Guidelines: Adhere strictly to the manufacturer’s installation instructions to ensure the crane is assembled correctly and safely.
- Alignment and Leveling: Pay close attention to the alignment and leveling of the crane components during installation, as improper installation can affect performance and safety.
- Electrical Installation: Ensure that all electrical installations are performed by qualified electricians and comply with local codes and standards.
- Commissioning and Testing
- Initial Testing: Conduct initial tests to verify that the crane is functioning correctly before putting it into operation. This includes no-load and full-load testing to check for any issues.
- Inspection and Certification: Have the crane inspected and certified by a qualified professional or regulatory body, if required, before it is put into regular use.
- Operator Training: Provide comprehensive training for operators on the new crane’s operation, emphasizing safety features and operational procedures.
- Documentation
- Operation Manuals: Ensure that all operation manuals, maintenance guides, and other documentation are handed over and reviewed with your team.
- Warranty and Service Information: Review warranty details and service agreements, and establish a schedule for regular maintenance and inspections.
Properly addressing these considerations can help ensure that your new overhead crane is delivered, installed, and commissioned with minimal disruption to your operations, setting the stage for safe and efficient use throughout its service life.
How do resale values of overhead cranes compare?
The resale value of overhead cranes can vary significantly based on a number of factors. Just like with any other piece of industrial equipment, certain attributes can either preserve the value of a crane over time or cause it to depreciate more rapidly. Here’s a look at some of the key factors that impact the resale values of overhead cranes:
- Brand and Manufacturer Reputation
- High-Quality Brands: Cranes manufactured by reputable brands known for quality, durability, and reliability tend to retain their value better than those from less known or lower-quality manufacturers.
- Age and Condition
- Age: Newer cranes generally have higher resale values than older ones, primarily due to less wear and tear and a longer remaining service life.
- Condition: A well-maintained crane in good working condition is more valuable than one that has been neglected or has visible damage, even if they are of the same age.
- Capacity and Specifications
- Higher Capacity: Cranes with higher lifting capacities often have higher resale values, as they can be used in a wider range of applications.
- Desirable Features: Specific features such as variable speed control, wireless operation, or advanced safety systems can enhance a crane’s resale value.
- Technological Advancements
- Modern Technology: Cranes equipped with the latest technology, such as automation features or energy-efficient designs, tend to retain value better than outdated models.
- Market Demand
- Industry Demand: The demand within specific industries can significantly impact resale value. If there’s a high demand for cranes in the construction, manufacturing, or shipping industries, for example, resale values will be higher.
- Geographical Demand: The location can also affect resale value, with certain regions having higher demand for cranes due to construction booms or industrial activities.
- Documentation and History
- Maintenance Records: Comprehensive maintenance and repair records can increase a crane’s resale value by demonstrating that it has been well cared for.
- Accident History: A crane that has been involved in accidents or has had significant repairs may have a lower resale value.
Comparative Resale Values
- Standard vs. Custom Models: Standard cranes that can be easily deployed in a variety of settings generally have better resale values compared to highly customized cranes, which may only suit specific applications.
- Electric vs. Diesel (if applicable): For cranes that come in different power options, electric cranes might have better resale value due to their lower operating costs and environmental benefits, depending on market trends and fuel prices.
While the depreciation rate of overhead cranes can be influenced by a multitude of factors, those that are well-maintained, from reputable manufacturers, with higher capacities and modern features, tend to hold their value better over time. The market demand, both in terms of industry and location, also plays a crucial role in determining the resale value of overhead cranes.
What are the insurance requirements for owning and operating overhead cranes?
Insurance for owning and operating overhead cranes is crucial to manage the financial risks associated with property damage, personal injury, or liability claims that can arise during crane operations. The specific insurance requirements can vary depending on the jurisdiction, the nature of the operations, and the risk assessment of the business. However, there are several types of insurance coverages that businesses owning and operating overhead cranes typically consider:
- Property Insurance
- Coverage: Protects against damage to the crane itself due to accidents, fires, theft, vandalism, or natural disasters.
- Consideration: The value of the crane and the cost to replace or repair it should be accurately reflected in the policy.
- General Liability Insurance
- Coverage: Provides protection against liability claims for bodily injury and property damage that occur on your business premises or as a result of your operations.
- Consideration: It’s essential for covering injuries to third parties or damage to third-party property, including when a crane accidentally drops a load causing injury or damage.
- Workers’ Compensation Insurance
- Coverage: Covers medical expenses, rehabilitation costs, and lost wages for employees who get injured on the job.
- Consideration: In many jurisdictions, workers’ compensation insurance is mandatory if you have employees. It’s particularly important in crane operations, which can pose significant risks to operators and other workers.
- Inland Marine Insurance
- Coverage: Provides protection for equipment and machinery while it is in transit or stored at a location other than the primary business premises.
- Consideration: This can be important if the crane is mobile and transported between different job sites.
- Umbrella Liability Insurance
- Coverage: Offers additional liability coverage beyond the limits of the general liability and auto liability policies. It can provide an extra layer of protection against large claims.
- Consideration: Given the high liability risks associated with crane operations, umbrella liability insurance can be a prudent investment.
- Equipment Breakdown Insurance
- Coverage: Covers the cost of repairing or replacing the crane if it breaks down due to mechanical failure, electrical arcing, or other covered incidents not typically included in standard property insurance.
- Consideration: This insurance can help minimize downtime and lost productivity due to equipment failures.
- Business Interruption Insurance
- Coverage: Compensates for lost income and covers operating expenses when business operations are disrupted due to a covered loss, such as damage to the crane.
- Consideration: Essential for maintaining financial stability during periods when the crane operations are halted for repairs or replacement.
Compliance and Risk Management
- Regulatory Requirements: Check local laws and regulations to ensure compliance with any mandatory insurance requirements for crane operations.
- Risk Assessment: Conduct a thorough risk assessment to identify potential hazards and liabilities associated with your crane operations, which can help in tailoring your insurance coverage to meet your specific needs.
It’s advisable to work with an insurance provider or broker who has experience in heavy equipment and construction-related policies to ensure comprehensive coverage that addresses all potential risks associated with owning and operating overhead cranes.